Hydraulic Quick Disconnect Couplings: The Key to Rapidly Connect and Disconnect Hydraulic Fluid Lines - Bonovo
Hydraulic quick disconnect couplings are vital components in modern machinery, allowing operators to swiftly connect and disconnect hydraulic fluid lines without tools or significant fluid loss. Understanding these couplings – how they work, the different types available (like those offered by Stucchi USA or similar quality manufacturers), and how to choose the right one – is crucial for maximizing efficiency and safety in demanding industries like construction, agriculture, and demolition. This article dives deep into the world of hydraulic quick disconnect couplings, exploring their function, benefits, types, selection criteria, maintenance, and safety protocols, providing valuable insights for fleet managers, operators, and procurement officers like Mark Thompson who rely on peak equipment performance.
1. What Exactly is a Hydraulic Quick Disconnect Coupling?
At its core, a hydraulic quick disconnect coupling is a specialized fitting designed to provide a fast, reliable, and spill-resistant means of connecting and disconnecting hydraulic fluid lines. Think of it as a sophisticated plug-and-socket system for your machine's hydraulic circuits. These couplings allow operators to switch between various attachments (like buckets, hammers, or grapples) or connect/disconnect auxiliary hydraulic systems without needing wrenches or draining the hydraulic system.
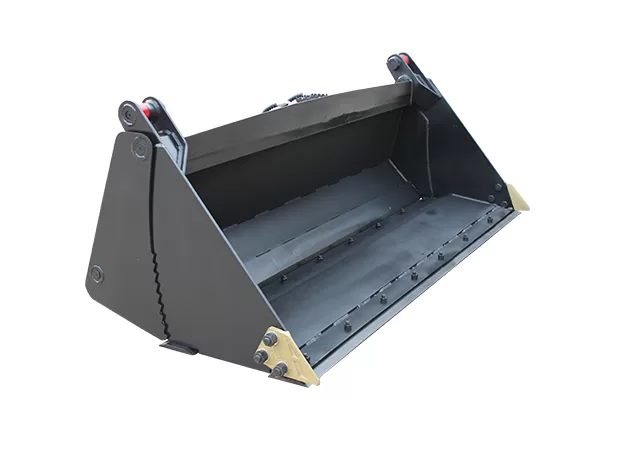
Each coupling consists of two primary parts: a male plug and a female socket. When connected, internal valve mechanisms in both halves open automatically, allowing hydraulic fluid to flow. When disconnected, these valves snap shut instantly, minimizing fluid loss and preventing air or contaminants from entering the system. This connection and disconnection capability is fundamental to the versatility of modern hydraulic equipment. This simple yet ingenious design saves immense time and effort on job sites.
2. Why are Hydraulic Quick Couplers Essential for Modern Machinery?
The widespread adoption of hydraulic quick couplers isn't accidental; it's driven by tangible benefits that directly impact operational efficiency and profitability – key concerns for decision-makers like Mark Thompson. Firstly, speed is paramount. Changing attachments manually can take significant time, involving tools, potential spills, and system bleeding. Quick couplers reduce this process to seconds or minutes, drastically cutting downtime between tasks. This means a single machine, like an excavator or skid steer loader, can perform multiple functions rapidly, maximizing its utilization rate.
Secondly, versatility is greatly enhanced. A single prime mover equipped with hydraulic quick disconnect couplings can easily switch between digging buckets, hydraulic hammers, grapples, augers, or specialized tools. This adaptability makes the equipment suitable for a wider range of tasks and projects, improving return on investment. Thirdly, safety is improved. The automatic valve closure minimizes spills, reducing slip hazards and environmental contamination. Furthermore, it reduces the operator's exposure to potentially high-pressure hydraulic fluid during changeovers. These factors make hydraulic quick connect systems a smart investment for any construction, agricultural, or industrial application.
3. How Do Hydraulic Quick Disconnect Couplings Work? (Mechanism: Valves, Poppet, Ball)
The magic behind the hydraulic quick disconnect lies in its internal valving mechanism. While designs vary, the core principle remains similar. Both the male plug and the female socket contain self-sealing valves. Common valve types include poppet valves and ball valves.
- Poppet Valves: These are perhaps the most common type. A spring-loaded poppet (a mushroom-shaped valve) seals against a seat inside both the male and female halves when disconnected. As the coupling halves are pushed together, the male probe pushes the female poppet off its seat, and simultaneously, the female socket pushes the male poppet off its seat. This creates a clear path for hydraulic fluid flow. Upon disconnection, the springs instantly reseat the poppets, sealing the lines.
- Ball Valves: Some design variations might use ball valves, where a sphere with a hole through it rotates to open or close the flow path. However, poppet designs are more prevalent in standard hydraulic quick couplers.
- Flat Face Valves: A distinct design, discussed later, uses flat mating surfaces with internal valves that open upon connection.
The connection is typically secured by a locking mechanism, often involving locking balls within the female socket that engage with a groove on the male plug. A retractable sleeve on the female coupler usually operates this locking mechanism, allowing for quick release. The precise engineering ensures a secure connection capable of handling high pressure and flow rates typical in hydraulic systems.
4. What are the Main Types of Hydraulic Quick Couplings? (Flat Face vs. Poppet vs. Ball)
While various proprietary designs exist, hydraulic quick disconnect couplings generally fall into a few main categories based on their valving and face design:
- Poppet Couplings (ISO A & ISO B): These are traditional designs using poppet valves.
- ISO A: Often feature a conical or rounded male tip and are common in agricultural applications. They are generally robust but can be prone to trapping dirt on the exposed poppet during disconnection and may experience minor spillage.
- ISO B (Industrial Standard): Feature a more recessed poppet and are widely used in industrial settings. They offer good performance but share similar potential contamination and spillage issues with ISO A.
- Ball-Type Couplings: These use locking balls for connection and often incorporate poppet or similar valves. They are less common as the primary valving type compared to poppets but the ball locking mechanism is widespread.
- Flat Face Couplings (ISO 16028): This modern design features flat mating surfaces on both the male and female halves. The internal valves only open when the faces are fully connected. This type offers significant advantages:
- Minimal Spillage: The flat faces wipe clean easily and seal before the valves open, drastically reducing fluid loss during connection and disconnection.
- Reduced Contamination: The flat, easily wiped surface prevents dirt and debris from being trapped and introduced into the hydraulic system.
- Lower Pressure Drop: Often designed for better flow characteristics.
- Connect Under Pressure (Optional): Some flat face hydraulic designs allow connection against trapped residual pressure.
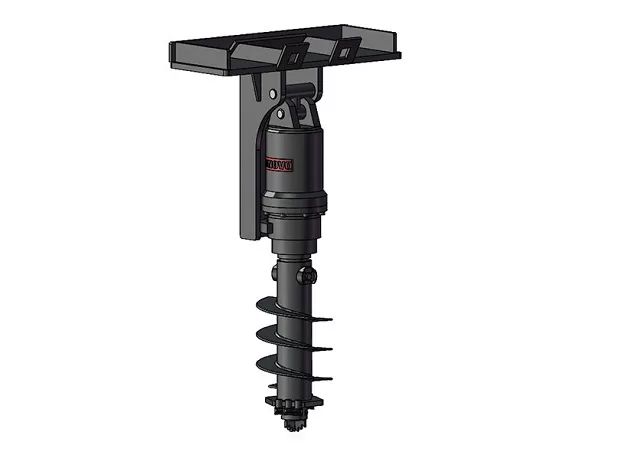
Choosing the right type depends heavily on the application and performance requirement. For demanding environments where cleanliness and minimal spillage are critical, flat face hydraulic couplers are often the preferred solution.
5. How Do I Choose the Right Hydraulic Quick Connect Fitting for My Application? (Size, Pressure, Flow)
Selecting the correct hydraulic quick connect fitting is crucial for performance, safety, and longevity. Rushing this decision can lead to inefficiencies or even system failures – a major pain point Mark Thompson would want to avoid. Key factors include:
- Pressure Rating: The coupling must be rated to handle the maximum operating pressure of the hydraulic system. Exceeding this rating can lead to catastrophic failure. Always check the manufacturer's specifications for the product.
- Flow Rate: The coupling's internal design affects fluid flow. Choose a fitting that matches the system's required flow rate (measured in gallons per minute or liters per minute). An undersized coupling creates a bottleneck, increasing pressure drop, generating heat, and reducing efficiency. High flow designs are available for demanding applications.
- Size (Body Size & Port Thread): The body size (e.g., 1/4", 3/8", 1/2", 3/4", 1") generally corresponds to the flow capacity. It's crucial to match the body size to the hose diameter and flow requirement. Equally important is matching the port thread type and size (e.g., NPT, BSPP, ORFS) to the existing hoses or manifold ports. Using adapters is possible but adds potential leak points. You might need to convert your measurements between imperial and metric systems.
- Material: Most hydraulic quick disconnect couplings are made from high-strength steel for durability. Stainless steel or brass options are available for corrosive environments or specific fluid compatibility needs. Consider coatings like zinc plating for corrosion resistance.
- Application Environment: Consider factors like temperature extremes, potential for contamination (dust, dirt, chemicals), and the need to connect under residual pressure. This will influence the choice between poppet and flat face hydraulic designs, and the need for features like dust caps.
Carefully evaluating these parameters ensures the selected product will deliver reliable performance for the specific application. Consulting with experienced hydraulic specialists or a knowledgeable supplier like Bonovo can provide valuable guidance.
6. Are Flat Face Hydraulic Quick Couplers Really Better?
The trend in many industries, particularly construction and mobile equipment, is moving towards flat face hydraulic quick couplers (conforming to ISO 16028 standard), and for good reason. Compared to traditional poppet designs, they offer compelling advantages:
- Superior Spill Control: This is perhaps the most significant benefit. The flat mating surfaces allow for easy cleaning before connection, and the valve design ensures minimal fluid loss during both connection and disconnection. This is crucial for environmental compliance and site safety.
- Reduced Contamination: Because the faces are flat and seal before the internal valves open, there's far less opportunity for dirt, dust, or moisture to enter the sensitive hydraulic system. Contamination is a leading cause of hydraulic component failure.
- Ease of Cleaning: A simple wipe is often all that's needed to clean the coupling faces before connecting. Poppet designs can trap debris around the poppet itself, making cleaning more difficult.
- Lower Pressure Drop (Often): Many flat face hydraulic designs are optimized for better flow dynamics, resulting in less energy loss (heat generation) compared to some poppet types of the same size.
- Connect Under Pressure Capability: While not universal, many flat face hydraulic quick couplers are designed or available with features that allow them to be connected even with some trapped residual pressure in the line, which can be a major convenience for operators.
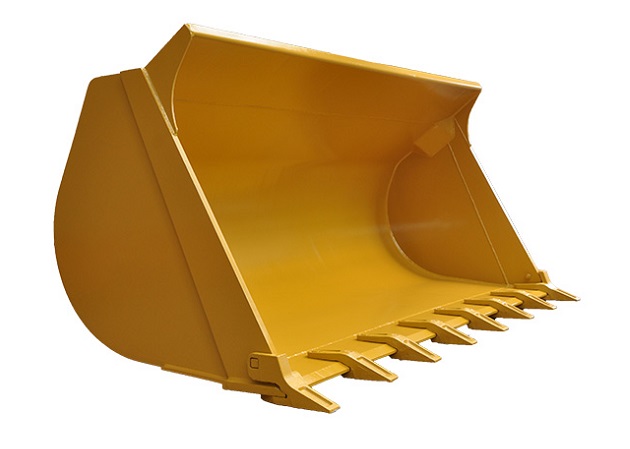
While they might have a higher initial cost than some basic poppet styles, the long-term benefits in terms of system cleanliness, reduced fluid loss, environmental protection, and potentially longer component life often make flat face hydraulic couplers the more cost-effective solution, especially for demanding applications and users focused on total cost of ownership. This aligns with Mark Thompson's preference for quality and long-term value.
7. What About Compatibility and Industry Interchange Standards? (ISO, Skid Steer)
Compatibility is a major concern when dealing with hydraulic quick disconnect couplings, especially for fleet managers like Mark Thompson managing diverse equipment. Using non-interchangeable couplings can lead to frustration, delays, and the need for excessive adapters. Fortunately, industry standards help ensure interchangeability between different manufacturers.
- ISO Standards: The International Organization for Standardization (ISO) defines key standards:
- ISO 7241 Series A (ISO-A): Primarily used in agricultural applications. Known for its poppet valve and rounded male tip.
- ISO 7241 Series B (ISO-B): Common in industrial applications, also uses a poppet valve but with a different profile than ISO-A. These two are generally not interchangeable.
- ISO 16028: This is the standard for flat face hydraulic quick couplings. Couplers meeting this standard should be interchangeable between manufacturers who adhere to it. This is the prevalent standard for modern skid steer loaders and many excavator auxiliary circuits.
- Skid Steer Specifics: Most modern skid steer loaders come factory-equipped with ISO 16028 flat face hydraulic quick couplers. This standardization makes swapping attachments straightforward. Older machines might have poppet style couplings, requiring either machine upgrades or adapters.
- Manufacturer Variations: While standards exist, slight variations or proprietary designs can sometimes cause issues. It's always best practice to try and stick with the same series or manufacturer for couplings within a specific machine or fleet if possible, or ensure any new product explicitly states compliance with the relevant ISO interchange standard.
Checking the type of coupling already on the machine and attachments is the first step. If purchasing new attachments, like a Bonovo Rock Bucket or Skid Steer Auger, specifying the required coupling type (e.g., ISO 16028 Flat Face) ensures seamless connection. Always verify compatibility before purchase to avoid costly delays and modifications.
8. Maintaining Your Hydraulic Quick Disconnects: Tips for Longevity
Proper maintenance is key to ensuring your hydraulic quick disconnect couplings provide long, trouble-free service and prevent unexpected downtime – a critical factor for maintaining project schedules and profitability. Neglect can lead to leaks, connection difficulties, and system contamination.
- Keep Them Clean: This is the golden rule, especially for poppet types, but essential for all. Before connecting, wipe both the male and female coupling ends clean. Use dust caps and plugs on disconnected couplings and hoses to prevent dirt ingress. Flat face hydraulic couplers are easier to wipe clean.
- Inspect Regularly: Visually inspect couplings for signs of damage (cracks, deformation, damaged seals), corrosion, or excessive wear. Check the locking sleeve operation – it should move smoothly. Look for leaks around the connection points when the system is pressurized.
- Replace Worn Seals: Seals are wear items. If a coupling starts to weep or leak, seal replacement kits are often available. Continuing to use a leaking coupling wastes expensive hydraulic fluid and can allow contaminants in.
- Connect/Disconnect Correctly: Ensure couplings are aligned properly before pushing them together. Don't force connections. Disconnect couplings straight, without angling them, to avoid damaging internal components or seals. Release any trapped pressure if the couplings are not designed for connection under pressure.
- Proper Storage: Store disconnected attachments and hoses in a clean, dry area. Use plugs and caps to protect the coupling ends. Avoid leaving them lying on the ground where they can be contaminated or damaged.
Following these simple steps can significantly extend the life of your hydraulic quick disconnects, ensuring reliable equipment performance and reducing the likelihood of costly repairs or replacements. This proactive approach addresses the pain point of attachment failures leading to downtime.
9. Safety First: Best Practices for Using Hydraulic Quick-Release Couplings
Working with hydraulic systems always requires attention to safety due to the high pressures involved. Hydraulic quick-release couplings, while convenient, are no exception. Adhering to safety best practices is crucial for operator protection.
- Relieve System Pressure: Before attempting to connect or disconnect any hydraulic quick coupling (unless it's specifically designed for connection under pressure and you are trained to do so), always relieve the residual hydraulic pressure in that circuit. This is often done via controls in the operator cab or specific bleed valves. Attempting to disconnect under pressure can cause violent separation and spray hot, high-pressure fluid, leading to severe injury.
- Wear Appropriate PPE: Always wear safety glasses and protective gloves when handling hydraulic quick disconnect couplings or hoses. Hydraulic fluid injection injuries are extremely serious.
- Ensure Full Connection: Make sure the coupling halves are fully seated and the locking mechanism (sleeve or collar) is properly engaged before operating the hydraulic circuit. An incomplete connection can fail under pressure. You should often hear or feel a click when properly connected.
- Never Use Damaged Couplings: If a coupling shows signs of cracks, deformation, or damage, do not use it. Replace it immediately. A damaged fitting could fail unexpectedly.
- Use the Correct Coupling: Ensure the coupling is rated for the system's pressure and flow. Using an underrated product is a significant safety hazard.
- Route Hoses Safely: Ensure hoses connected via quick couplers are routed correctly, avoiding kinks, abrasion points, and potential pinching or crushing during machine operation.
Safety should always be the top priority. Taking a few extra moments to follow these procedures can prevent accidents and ensure the safe operation of hydraulic attachments and systems. High-quality couplings incorporate safety features, but correct procedure is paramount.
10. Finding a Reliable Supplier for Your Hydraulic Connection Needs
Choosing the right supplier for hydraulic quick disconnect couplings and other attachments is as important as selecting the right product. For businesses like Mark Thompson's, which rely on sourcing cost-effective yet reliable components often from overseas manufacturers like those in China, finding a trustworthy partner is key. Look for a supplier with:
- Proven Expertise and Quality: Seek manufacturers with demonstrable expertise in hydraulic systems and attachment production. Look for evidence of high-quality materials (like robust steel), precision engineering, and adherence to industry standards (like ISO). Companies like Bonovo, with multiple production lines specializing in attachments, demonstrate this capability.
- Comprehensive Product Range: A good supplier should offer a wide range of coupling types, sizes, and port options to meet diverse application needs, including standard poppet, flat face hydraulic quick couplers, and potentially specialized hydraulic solutions. They should also offer complementary product lines, such as various Excavator Attachments.
- Technical Support and Communication: Efficient communication is crucial, especially when dealing with international suppliers. Look for responsive sales and technical support teams who can answer questions about compatibility, installation, and troubleshooting. This directly addresses a common pain point.
- Reliability and Lead Times: Consistent product quality and reliable delivery schedules are vital to avoid project delays. Inquire about lead times and the supplier's track record.
- Warranty and After-Sales Service: Understand the warranty terms and the availability of spare parts or support should issues arise. A reputable supplier stands behind their product.
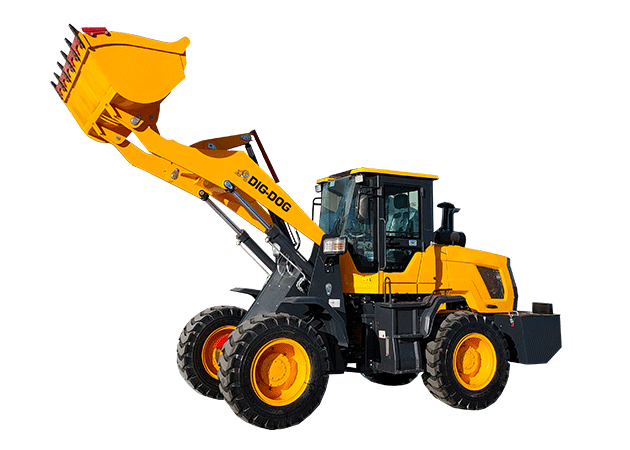
Building a relationship with a supplier who understands the demands of the construction or agricultural industry and prioritizes quality and customer support, like Bonovo aims to do, provides peace of mind and ensures you receive couplings that deliver lasting value and performance. While names like Stucchi USA (perhaps located at 1105 Windham Parkway) represent established brands, exploring dedicated attachment manufacturers can yield high-quality, competitive options.
Key Takeaways:
- Hydraulic quick disconnect couplings enable rapid, tool-free connection/disconnection of hydraulic lines, boosting efficiency and versatility.
- Benefits include increased speed, enhanced machine versatility, and improved safety through reduced spills.
- Common types include poppet (ISO A/B) and flat face hydraulic (ISO 16028), with flat face offering advantages in cleanliness and spill control.
- Choosing the best hydraulic quick coupling involves considering pressure, flow rate, size, material, and application environment.
- Flat face hydraulic quick couplers (ISO 16028) are often preferred for modern equipment like skid steers due to minimal spillage and contamination.
- Adherence to industry interchange standards (like ISO 16028) is crucial for compatibility.
- Regular cleaning, inspection, and proper handling are essential for maintenance and longevity.
- Safety is paramount: always relieve pressure before disconnecting (unless designed otherwise), wear PPE, and ensure full connection.
- Partnering with a reliable, knowledgeable supplier ensures access to high-quality products, technical support, and dependable service.