Mastering Hydraulic Quick Couplers: A Comprehensive Guide to Identifying Different Types of Hydraulic Quick Connect Fittings - Bonovo
Hydraulic quick couplers are unsung heroes in the world of heavy machinery. They allow for swift and efficient connection and disconnection of hydraulic lines, which is absolutely vital for versatile equipment like excavators, skid steer loaders, and wheel loaders. If you're like Mark Thompson, a savvy fleet manager or construction company owner in the USA, you understand that minimizing downtime and maximizing your equipment's utility is key to profitability. This article, brought to you by Allen from Bonovo, a leading factory in China specializing in excavator attachments and machinery, will delve deep into the world of hydraulic quick couplers. We'll explore how to identify hydraulic quick couplers, understand the different types of hydraulic quick couplings, and ensure you're making the best choices for your hydraulic system. Knowing your couplings isn't just about convenience; it's about safety, efficiency, and protecting your investment. This guide is worth reading because it will empower you to make informed decisions, avoid costly mistakes, and keep your operations running smoothly.
What Exactly is a Hydraulic Quick Coupler and Why is it Essential for Your Machinery?
A hydraulic quick coupler is a specialized fitting designed to quickly connect and disconnect hydraulic hoses without the need for tools and, crucially, with minimal loss of hydraulic fluid. Think of it as a sophisticated plug-and-socket system for your machinery's circulatory system. The coupler consists of two halves: a male end (nipple or plug) and a female end (socket or coupler body). When connected, they form a secure, leak-proof seal, allowing hydraulic fluid to flow under pressure to power attachments or implements. For businesses like Mark's, which rely on the versatility of their equipment—switching between buckets, hammers, grapples, and augers—the ability to make these changes rapidly is a game-changer.
The essential nature of a hydraulic quick coupler stems from its ability to significantly reduce downtime. Imagine manually unbolting and re-bolting hydraulic lines every time you need to change an attachment. It's time-consuming, messy, and increases the risk of introducing contaminants into the hydraulic system. A quick coupling transforms this process into a matter of seconds or minutes. This speed directly translates to increased productivity on the job site. Furthermore, modern couplers are designed to minimize spillage and air inclusion, protecting both the environment and the integrity of the hydraulic system. From my perspective as Allen, representing a factory that produces a wide range of these attachments, we see firsthand how integral reliable hydraulic quick connect solutions are to our customers' success. They are not just a convenience; they are a cornerstone of operational efficiency.
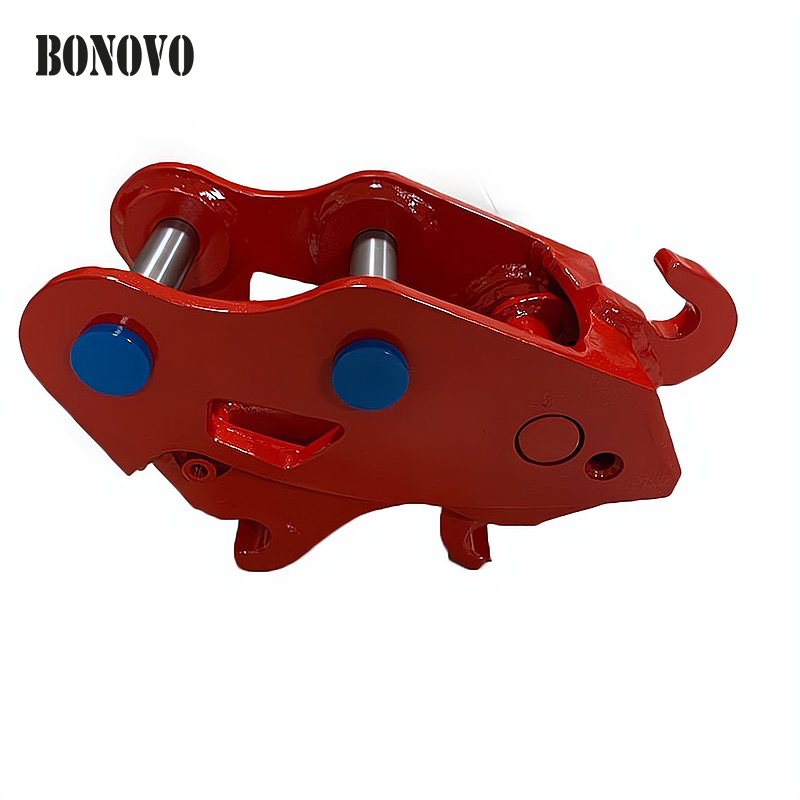
How Do Different Types of Hydraulic Quick Couplers Vary in Design and Mechanism?
The world of hydraulic quick couplers is diverse, with several distinct designs, each tailored for specific applications and performance requirements. The primary variation lies in the internal valve mechanism that seals the hydraulic lines when the coupler is disconnected and opens to allow flow when connected. Understanding these differences is the first step to correctly identify hydraulic quick couplers. The most common types of hydraulic quick couplers you'll encounter are poppet-style, flat face (or dry-break), ball-lock, and pin-lock couplings.
Each design impacts factors like flow rate, pressure handling capabilities, ease of connection (especially under residual pressure), and the amount of spillage during connection and disconnection. For instance, a poppet valve coupler might be more tolerant of minor misalignments but could experience more fluid loss than a flat face coupler. The materials used in construction also vary, influencing durability and resistance to corrosive environments. As a manufacturer, we at Bonovo pay close attention to these design nuances because they directly affect the performance and longevity of the attachments our couplers serve, such as our versatile skid steer auger attachments. Knowing the different types of hydraulic quick mechanisms is crucial for selecting the right fitting for your needs.
The Poppet Valve Hydraulic Coupler: A Closer Look at a Common Choice
The poppet valve hydraulic coupler is one of the most traditional and widely used designs. Its mechanism involves a spring-loaded poppet valve in both the male and female halves. When the coupler is disconnected, these poppets seal against a seat, preventing hydraulic fluid from escaping. Upon connection, the male and female poppets push against each other, unseating both valves and allowing fluid to flow. This design is often favored for its relatively simple construction and cost-effectiveness.
However, poppet couplers do have some drawbacks. They can be prone to a small amount of spillage during connection and disconnection of fluid lines, and they can also allow air to be introduced into the hydraulic system if not connected carefully. This can be a concern for sensitive hydraulic components. Despite these points, their robust nature and wide availability make them a common sight in many hydraulic applications, particularly where minor fluid loss is acceptable and cost is a significant driver. Many older pieces of equipment, including some tractor implements, utilize this type of hydraulic coupler.
Why are Flat Face Hydraulic Couplers Becoming the Industry Standard?
Flat face hydraulic couplers, often referred to as dry-break or non-spill couplings, are rapidly gaining popularity and are considered the industry standard in many demanding applications. As the name suggests, the mating surfaces of these couplers are flat. This design offers several significant advantages. Firstly, they achieve a virtually leak-free connection and disconnect, minimizing fluid loss and environmental contamination. This is a huge plus for companies like Mark's, aiming for cleaner and safer work environments.
Secondly, the flat face design significantly reduces the chance of air inclusion into the hydraulic system during connection. This is critical for protecting sensitive hydraulic components from cavitation and ensuring consistent performance. Thirdly, flat face couplers are much easier to clean before connection, reducing the risk of dirt and debris entering the system—a major cause of premature wear and component failure. Many flat face quick couplings conform to the ISO 16028 standard, ensuring interchangeability between different manufacturers. While they might have a higher initial cost than poppet couplers, the long-term benefits in terms of system cleanliness, safety, and reduced fluid loss often make them a more economical choice for heavy duty operations.
- Benefits of Flat Face Couplers:
- Minimal spillage (near zero)
- Reduced air inclusion
- Easy to clean mating surfaces
- Lower risk of system contamination
- Often ISO standardized (e.g., ISO 16028) for interchangeability
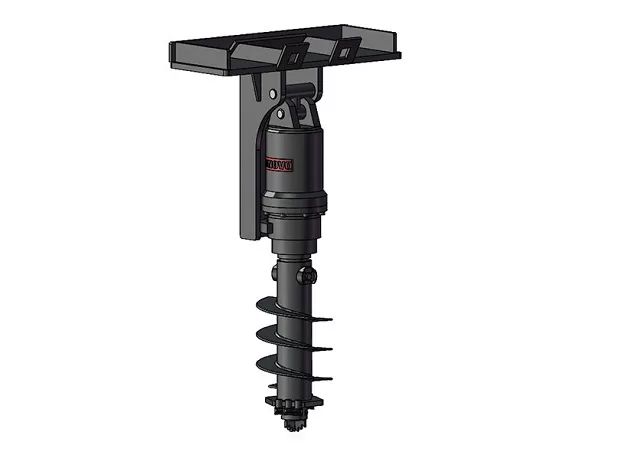
Exploring Ball-Lock and Pin-Lock Couplers: What Are Their Niche Applications?
Beyond poppet and flat face couplers, you might also encounter ball-lock and pin-lock couplings, though they are often found in specific or less demanding hydraulic applications, and sometimes more in pneumatic systems. Ball-lock couplers use a series of ball bearings in the female coupler that retract to allow the male half to be inserted. Once inserted, the balls engage with a groove on the male fitting, securing the connection. This quick connection mechanism is simple and often used for lower pressure hydraulics and general industrial applications.
Pin-lock couplers, on the other hand, typically use one or more robust pins to secure the connection. These are less common in general hydraulics but can be found in specialized, heavy duty applications where a very secure, positive lock is required, sometimes in older designs or custom equipment. While not as prevalent as poppet or flat face types for mainstream hydraulic attachments, understanding that these different quick coupling mechanisms exist helps in identifying less common hydraulic connections you might come across.
Decoding Threads: How Do I Identify the Thread Type on My Hydraulic Coupler?
One of the most critical aspects of selecting or replacing a hydraulic quick coupler is ensuring the thread type matches your existing hydraulic hoses or equipment ports. Mismatched threads can lead to leaks, damaged couplings, and even dangerous high-pressure blowouts. As Allen, I've seen my share of issues caused by incorrect thread identification, and it's a pain point we help customers like Mark avoid. The most common thread types in hydraulics include:
- NPT/NPTF (National Pipe Thread/National Pipe Thread Fuel): Tapered threads common in North America.
- BSPP (British Standard Pipe Parallel): Parallel threads common in Europe, Asia, and Australia, requiring a bonded seal or O-ring.
- BSPT (British Standard Pipe Tapered): Tapered threads, similar to NPT but with different thread angles and pitches.
- JIC (Joint Industry Council) / SAE 37° Flare: A popular fitting with a 37-degree flared seating surface.
- ORFS (O-Ring Face Seal): Provides an excellent leak-free connection using an O-ring in a groove on the flat face of the male fitting.
To identify a thread, you'll typically need a set of calipers to measure the outside diameter (for male threads) or inside diameter (for female threads) and a thread pitch gauge to determine the number of threads per inch or the distance between threads (for metric). Comparing these measurements against thread identification charts is the most reliable way. "Eyeballing" a thread is a recipe for disaster! Always ensure your hydraulic fitting has the correct thread for a secure and reliable hydraulic seal. Many couplers are designed with specific thread options to match regional preferences and equipment standards.
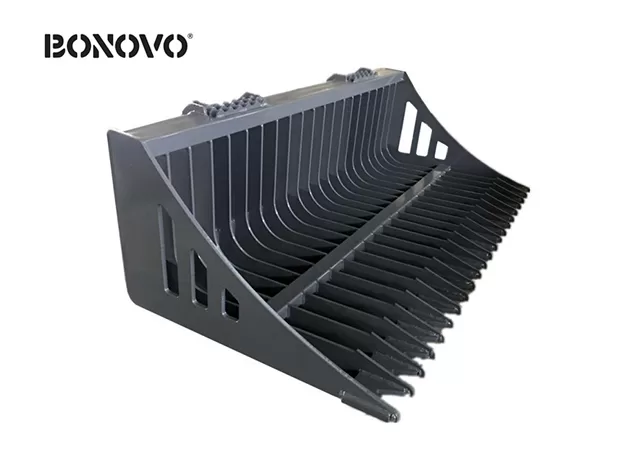
ISO Standards Demystified: Why Do They Matter for Hydraulic Quick Couplers and Interchangeability?
ISO (International Organization for Standardization) standards play a vital role in the world of hydraulic quick couplers. These standards define dimensions, performance requirements, and testing procedures for various types of hydraulic quick couplers. For end-users like Mark Thompson, ISO standards are incredibly beneficial because they promote interchangeability. This means that a hydraulic quick coupler from one manufacturer that complies with a specific ISO standard (e.g., ISO 7241 Series A, ISO 7241 Series B, or ISO 16028 for flat face couplers) should, in theory, be compatible with a mating coupler half from another manufacturer adhering to the same standard.
This interchangeability simplifies sourcing spare parts, allows for more flexibility in equipment selection, and can help avoid being locked into a single supplier. For us at Bonovo, your trusted factory partner, adhering to relevant ISO standards where applicable is part of our commitment to quality and customer satisfaction. It ensures that our products meet globally recognized benchmarks for performance and reliability. When you see an ISO designation on a hydraulic coupler, it provides a level of assurance regarding its design and potential compatibility. Always verify the specific ISO series, as different series (like A and B under ISO 7241) are not interchangeable with each other, even if they are both "poppet" style.
ISO Standard | Common Coupler Type | Key Feature |
---|---|---|
ISO 7241 Series A | Poppet | General purpose, widely used |
ISO 7241 Series B | Poppet | Industrial, often higher pressure than Series A |
ISO 16028 | Flat Face | Low spillage, flush face, high performance |
ISO 5675 | Ball/Poppet | Agricultural equipment (e.g., tractor use) |
This table gives a quick overview, but always check the specific details of the coupler and its intended application.
Are There Specialized Hydraulic Couplers Designed for High-Pressure Scenarios?
Absolutely. Standard hydraulic quick couplers have defined pressure ratings, but many applications, especially in heavy duty construction, demolition, and mining, operate at significantly high pressure. For these scenarios, specialized high-pressure hydraulic quick couplers are essential. These couplers are designed with robust materials, stronger locking mechanisms, and advanced sealing technologies to safely handle pressures that can exceed 5000 PSI (350 bar) or even reach 10,000 PSI (700 bar) and beyond in some cases.
Using a standard coupler in a high-pressure system is extremely dangerous and can lead to catastrophic failure, equipment damage, and serious injury. High-pressure couplers often feature specific design elements like reinforced bodies, special valve designs to minimize flow restriction at high pressures, and materials selected for their high tensile strength and fatigue resistance. When sourcing couplers for equipment like a powerful hydraulic hammer, which can generate significant pressure spikes, it's crucial to verify that the hydraulic quick coupler types are rated for the maximum operating pressure of your hydraulic system. Always check the manufacturer's specifications for the coupler and the equipment.
Troubleshooting 101: Common Problems and Maintenance Tips for Your Hydraulic Quick Couplers
Even the best hydraulic quick couplers can experience issues if not properly maintained or if they are used beyond their design limits. Mark Thompson, like many fleet managers, knows that attachment failures and downtime are major pain points. Understanding common problems and practicing good maintenance can significantly extend the life of your couplings and prevent unexpected breakdowns.
Common Problems:
- Leaks: Can be caused by worn seals, damaged mating surfaces, incorrect thread connections, or exceeding pressure ratings.
- Difficulty in Connection/Disconnection: Often due to residual pressure trapped in the hydraulic line, dirt or debris in the coupler, or damaged internal components. Some multiple hydraulic quick coupler blocks are designed to relieve this pressure.
- Failure to Connect/Disconnect: Could be due to severe damage, incompatible halves, or a jammed locking mechanism.
- Premature Wear: Caused by contamination, frequent connection/disconnection under high pressure or flow, vibration, or using the wrong coupler type for the application.
- Spillage during connection and disconnection of fluid lines: While some spillage is expected with poppet couplers, excessive spillage indicates a problem. Flat-face quick couplings are designed to minimize this.
Maintenance Tips:
- Keep them Clean: Always wipe both male and female halves of the coupler before connection. Use a dust cap and plug on disconnected couplers to prevent contamination.
- Inspect Regularly: Look for signs of wear, damage (dents, cracks, corrosion), or leaking seals. Replace damaged couplers immediately.
- Relieve Pressure: Before attempting to connect or disconnect hydraulic lines, always relieve any trapped hydraulic pressure in the system and the attachment lines.
- Lubricate (If Recommended): Some couplers benefit from a light lubrication of the seals or locking mechanism with a compatible hydraulic fluid or grease. Check manufacturer guidelines.
- Ensure Proper Alignment: Avoid forcing connections. If a coupler doesn't connect smoothly, investigate the cause.
- Use Genuine Spare Parts: When replacing seals or other components like durable excavator bucket pins, use parts recommended by the coupler manufacturer to ensure compatibility and performance.
- Understand Warranty Terms: When purchasing, clarify warranty and after-sales service for your couplings, especially if sourcing internationally. This is a key concern for buyers like Mark.
"A few minutes spent on daily inspection and cleaning of your hydraulic quick couplers can save hours of downtime and thousands in repair costs down the line," I often tell my clients. It’s simple advice, but incredibly effective.
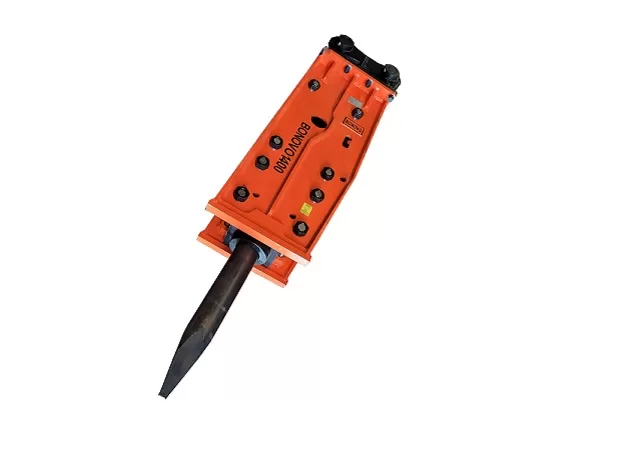
Making the Right Choice: How Can I Ensure I'm Selecting the Perfect Hydraulic Coupler for My Equipment?
Choosing the right hydraulic quick coupler is not a one-size-fits-all decision. It requires careful consideration of several factors to ensure optimal performance, safety, and longevity. For someone like Mark Thompson, who is quality-sensitive yet seeks competitive pricing, making an informed choice is paramount. Here are key factors to consider:
- Pressure Rating: The coupler must be rated for the maximum operating pressure of your hydraulic system, including any potential pressure spikes. This is non-negotiable for safety.
- Flow Rate: The coupler should be sized to handle the required flow rate without causing excessive pressure drop or heat generation. An undersized coupler can starve your attachments.
- Fluid Compatibility: Ensure the coupler materials (body and seals) are compatible with the type of hydraulic fluid being used in your system (e.g., mineral oil, synthetic fluids, biodegradable fluids).
- Operating Environment: Consider temperature extremes, potential for corrosive substances, dust, and vibration. This will influence material selection (e.g., steel, stainless steel, brass) and seal types.
- Type of Coupler: Decide between poppet, flat face, or other types based on your needs for spillage control, contamination prevention, and ease of connection. For most modern, demanding applications, a flat face type is often preferred.
- Thread Type and Size: Ensure the coupler thread matches your hydraulic hoses and ports. This involves identifying the correct sizes and types (e.g., NPT, BSPP, JIC, ORFS).
- Interchangeability (ISO Standards): If compatibility with existing equipment or other brands is important, look for couplers that adhere to relevant ISO standards.
- Connection/Disconnection Force: Consider how easy the coupler is to connect and disconnect, especially if it needs to be done frequently or under slight residual pressure. Some push to connect couplers offer easier operation.
- Application Specifics: The type of machinery (excavator, skid steer, tractor) and the attachments being used can influence the best hydraulic quick coupler types.
- Supplier Reliability: This is a big one for Mark. Work with reputable suppliers who can provide technical support, clear specifications, reliable lead times, and good after-sales service, including warranty and spare parts. As a factory like Bonovo, we pride ourselves on clear communication and standing behind our products, like our high-quality mechanical quick coupler.
Don't hesitate to consult with coupler manufacturers or knowledgeable suppliers. Providing details about your equipment and application will help them recommend the most suitable connection solutions. It's always better to ask questions upfront than to deal with compatibility issues or failures later.
Key Takeaways for Mastering Hydraulic Quick Couplers:
- Understand the Basics: A hydraulic quick coupler allows for rapid, tool-free connection and disconnection of fluid lines, saving time and boosting efficiency.
- Know Your Types: The main types of hydraulic quick couplers are poppet, flat face, ball-lock, and pin-lock, each with distinct advantages and applications. Flat face couplers (often ISO 16028) are preferred for low spillage and cleanliness.
- Thread Identification is Crucial: Always correctly identify and match thread types (NPT, BSPP, JIC, etc.) to prevent leaks and damage.
- ISO Standards Matter: ISO standards promote interchangeability and ensure a certain level of quality and performance.
- Match Coupler to Application: Consider pressure, flow rate, fluid compatibility, and operating environment when selecting a coupler.
- Maintenance is Key: Regular cleaning, inspection, and relieving pressure before connection/disconnection will extend coupler life and prevent issues.
- Prioritize Safety: Always use couplers rated for your system's pressure and never force a connection.
- Consult Experts: When in doubt, speak with manufacturers or experienced suppliers to ensure you choose the right hydraulic quick release couplings for your specific needs.
By understanding these aspects, you can effectively identify hydraulic quick couplers, make informed purchasing decisions, and ensure your heavy machinery operates at peak performance and safety.