Maximize Your Excavator's Power: The Ultimate Guide to the Backhoe Thumb Attachment - Bonovo
Ever watched an excavator try to pick up a tricky log or a pile of loose branches? It can be like trying to eat spaghetti with just a fork – a lot of things slip away! But what if your excavator had a "thumb" to help it grab things? That's exactly what an excavator thumb attachment does. This guide is all about these amazing tools. We'll explore what a thumb for excavator is, how it works, and why it's a game-changer for anyone who uses an excavator or backhoe. If you want to make your machine more helpful and get more work done, then learning about an excavator thumb is definitely worth your time!
As someone who has been manufacturing excavator attachments for many years, I'm Allen, and my company in China specializes in creating these tools for customers all over the world, including the USA, Europe, and Australia. I've seen firsthand how the right attachment, like a sturdy thumb, can transform an excavator from a simple digging machine into a multi-talented workhorse. We'll dive into the different types of thumbs, how to choose the best one, and how they can make your jobs easier and more profitable.
1. What is an Excavator Thumb, and Why is it a Must-Have Attachment?
Imagine your hand. You can pick up almost anything because you have fingers and a thumb that work together. An excavator thumb works in a very similar way for your excavator or backhoe. It's a strong metal attachment that mounts onto the excavator’s stick (the part of the arm that holds the bucket). This thumb works with the excavator’s bucket to create a grabbing or clamping action. Think of the bucket as the fingers and the thumb as, well, the thumb!
So, why is this thumb attachment a must-have? Without a thumb, an excavator is great at digging holes or scooping loose dirt. But try picking up a rock, a tree stump, or a pile of pipes, and things get tricky. The load can easily roll off or out of the bucket. A thumb for excavator presses against the bucket, holding objects securely. This means you can lift, move, and place items with much more precision and safety. For many of our customers, from construction companies to landscapers, adding a thumb is one of the first upgrades they make to their excavator or tractor-mounted backhoe. It instantly expands what their machine can do, saving time and effort on the job site.
Many operators tell us that once they've used an excavator with a thumb, they can't imagine going back. It's like suddenly having an extra, very strong hand on their machine. This simple attachment adds so much value by making the excavator far more versatile. It’s not just for big construction jobs; even a compact excavator used for landscaping can benefit hugely from a thumb. The ability to easily grab and manipulate various objects is a real game-changer.
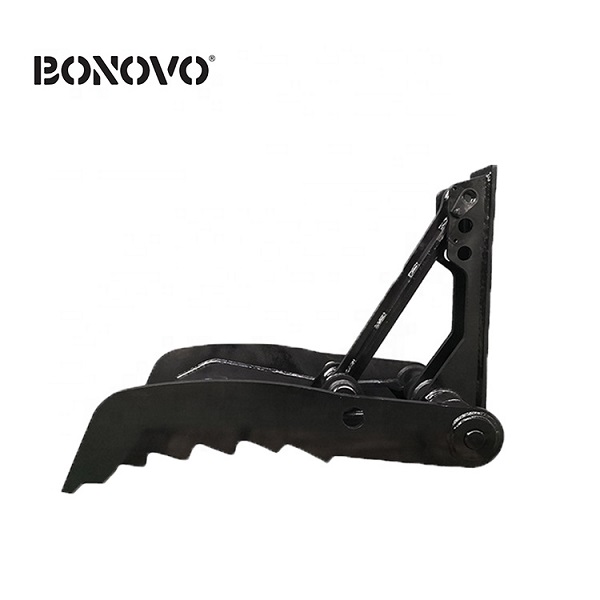
2. How Can an Excavator Thumb Improve Your Machine's Functionality on Site?
An excavator thumb dramatically boosts your machine's functionality in several key ways. Firstly, it significantly improves material handling capabilities. Whether you're clearing land and need to move logs and brush, or working on a demolition site and need to sort debris, a thumb allows your excavator to securely grab and hold onto these awkwardly shaped items. This means fewer dropped loads, faster cycle times, and a cleaner, more organized job site. The operator can work with more confidence, knowing the material is secure.
Secondly, a thumb enhances the precision of your excavator. When placing items like rocks for a retaining wall or pipes in a trench, the thumb provides the control needed to position them accurately. This reduces the need for manual labor to adjust materials, which not only saves time but also improves safety for ground crews. The ability to gently manipulate objects with the excavator’s bucket and thumb combination is invaluable. We often hear from our clients, especially those in landscaping and utility work, how much this added precision helps them achieve a higher quality finish.
Finally, adding a thumb increases the overall efficiency and productivity of your excavator. Tasks that would have been slow and difficult, or might have even required a second machine or more manpower, can now be handled quickly by a single excavator equipped with a thumb. This means more work done in less time, which directly impacts the profitability of a project. For businesses looking to get the most out of their equipment investment, an excavator thumb is a relatively low-cost attachment that delivers a big return by enhancing the machine’s core functionality.
3. Choosing Your Grip: Is a Mechanical Thumb or a Hydraulic Thumb Better for Your Excavator?
When you decide to get a thumb for your excavator, one of the first big choices is whether to go for a mechanical thumb or a hydraulic thumb. Both types of excavator thumb have their pros and cons, and the best one for you depends on your needs and how you plan to use your excavator or backhoe.
A mechanical thumb, sometimes called a "rigid" or "stiff-arm" thumb, is the simpler of the two. It's usually set in a few fixed positions using a pin and a strut, or it can be manually adjusted. To change the thumb’s position relative to the bucket, the operator often has to get out of the cab and make the adjustment. Mechanical thumbs are generally less expensive upfront and have fewer moving parts, which can mean less maintenance. They are a good, cost-effective option for occasional use or if you mostly handle materials of a similar size. Many smaller tractor units or mini-excavators start with a mechanical thumb because it’s a straightforward solution.
A hydraulic thumb, on the other hand, offers much more flexibility and control. It's connected to the excavator's hydraulic system, allowing the operator to open and close the thumb from inside the cab using a joystick or pedal. This means you can constantly adjust the thumb’s grip on the fly, making it perfect for handling various objects of different shapes and sizes. A hydraulic excavator thumb provides a much stronger and more consistent clamping force. While a hydraulic thumb is more expensive and has a more complex installation, the increased productivity and ease of use often make it a worthwhile investment for those who will use the thumb frequently or for a wide range of tasks like demolition or complex material handling. For a truly versatile excavator, a hydraulic thumb is often the preferred choice.
Here's a quick comparison:
Feature | Mechanical Thumb | Hydraulic Thumb |
---|---|---|
Control | Manual adjustment, fixed positions | Full control from cab, variable grip |
Cost | Lower initial cost | Higher initial cost |
Complexity | Simpler design, fewer parts | More complex, requires hydraulics |
Versatility | Good for consistent loads | Excellent for varied loads |
Operator Effort | Requires getting out to adjust | Adjusted easily from cab |
Best For | Occasional use, budget-conscious | Frequent use, maximum productivity |
Ultimately, choosing the right thumb depends on your specific excavator model, the types of jobs you do, and your budget.
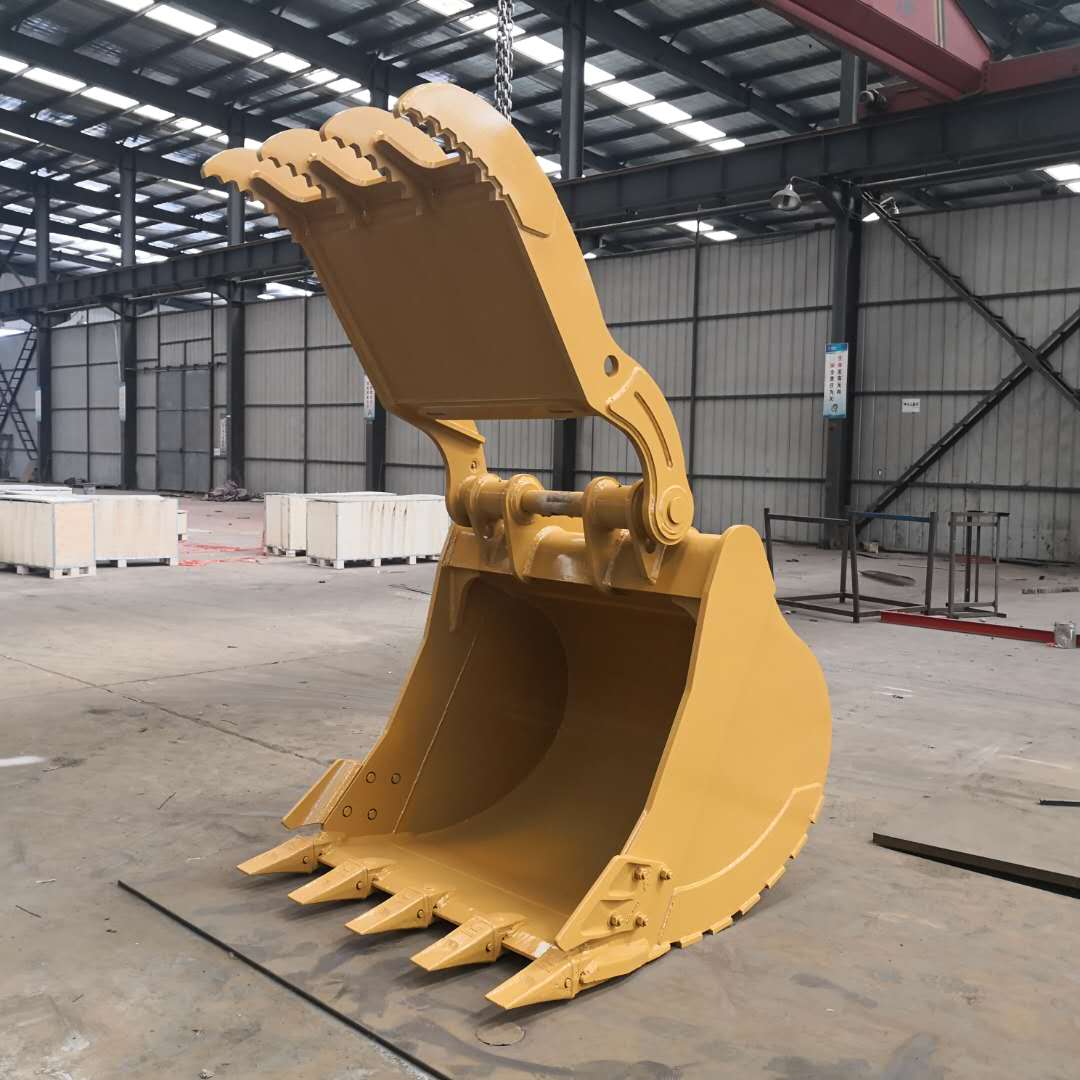
4. Why Does the Quality of Your Excavator Thumb Matter for Tough Jobs?
When you're dealing with tough jobs like demolition, rock handling, or clearing dense brush, the quality of your excavator thumb is super important. A thumb is constantly under stress, gripping, crushing, and moving hefty materials. If it's made from low-quality steel or has a poor design, it can bend, crack, or break, leading to dangerous situations, costly downtime, and frustrating project delays. This is a common concern for equipment owners like Mark Thompson, who need reliable attachments. A well-built thumb made from high-strength, wear-resistant steel (like AR400 or AR500) will withstand the toughest conditions and last much longer.
At our factory, we understand that durability is key. That's why we focus on using heavy-duty materials and robust construction techniques for every thumb we manufacture. The weld quality is also critical. Strong, professional welds ensure that the thumb components, like the tines and the main bracket, stay securely connected even under extreme pressure. A high-quality excavator thumb will also have features like reinforced stress points and hardened pins, which contribute to its overall strength and longevity. Investing a bit more in a quality thumb upfront can save you a lot of money and headaches in the long run by reducing repairs and replacement costs.
Think about it: your excavator is a powerful machine, and the thumb attachment needs to be able to match that power. A flimsy thumb won't just fail; it could also damage your excavator’s bucket or stick. When you're choosing an excavator thumb, don't just look at the price. Ask about the steel grade, the design features, and the manufacturer's reputation. A good quality thumb makes all the difference in performance and reliability, especially when the going gets tough. It ensures your operator can work efficiently and safely, tackling demanding tasks with confidence. These thumbs are engineered for robust performance.
5. Getting it Right: How Do You Safely Weld and Install an Excavator Thumb?
Installing an excavator thumb, especially a weld-on thumb, needs to be done correctly and safely. While some thumbs are "pin-on" and use existing pin locations on the excavator arm, many heavy-duty thumbs require a base plate to be welded directly onto the excavator’s stick or dipper. This weld is super important because it's what holds the thumb securely to your machine. If the weld is weak or done improperly, the thumb could break off during operation, which is extremely dangerous.
First, preparation is key. The area on the excavator stick where the thumb’s mounting bracket will be welded needs to be super clean. Grind off any paint, rust, or grease. This helps ensure a strong, clean weld. Next, you need to position the thumb correctly. It should be able to fold neatly against the stick when not in use and reach the bucket’s teeth or cutting edge when fully extended. It's a good idea to tack weld the bracket in place first, then cycle the bucket and stick through their full range of motion to check for any interference. You want to measure your bucket and the stick to find the optimal placement for the thumb.
When it comes to the actual welding, it’s best to have it done by a qualified welder who understands how to weld heavy steel and the specific requirements for excavator attachments. Using the right type of welding rod or wire (like a MIG welder with appropriate wire for high-strength steel) and proper welding techniques (like pre-heating if necessary for certain steels) is crucial for a strong, durable weld. After welding, inspect the weld carefully for any cracks or defects. For a hydraulic thumb, you'll also need to connect the hydraulic lines, making sure they are routed safely and won't get pinched or snagged during operation. Taking the time and effort to install your excavator thumb correctly will ensure it performs well and keeps your operator safe. Many manufacturers provide a kit with detailed instructions, but if you're not confident, professional installation is always the best choice for these weld-on thumbs.
6. Can a Simple Thumb Attachment Truly Maximize Your Excavator’s Versatility?
Absolutely! It might seem like a simple piece of metal, but a thumb attachment can dramatically maximize your excavator’s versatility. Think of your excavator without a thumb as a machine that can only scoop and dig. That’s useful, for sure, but it’s limited. Once you attach a thumb, your excavator gains the ability to grab, hold, sort, and place a huge variety of materials. It’s like giving your machine a hand.
This newfound ability opens up a whole new world of tasks your excavator can tackle. On a construction site, it can easily handle debris removal, place rocks for landscaping, or move pipes and lumber. For forestry work, an excavator with a thumb can load logs, clear brush, and manage stumps. In demolition, it becomes an indispensable tool for tearing down structures and sorting materials for recycling. Even on a farm, a backhoe or compact excavator with a thumb can help with tasks like clearing fence lines or moving bales. The excavator’s versatility is boosted so much that it can often reduce the need for other specialized equipment or extra manual labor.
The integration of a thumb, whether it's a mechanical thumb or a hydraulic thumb, transforms the excavator into a multi-purpose tool. This means one machine can do the job of several, saving you money on equipment rentals or purchases, and reducing the number of machines you need to transport to a job site. As a manufacturer, we've seen countless customers, from small landscaping businesses to large construction firms, report significant increases in productivity and the range of services they can offer after adding a thumb for excavator. It’s a relatively small investment that unlocks a huge amount of potential in your existing excavator or tractor.
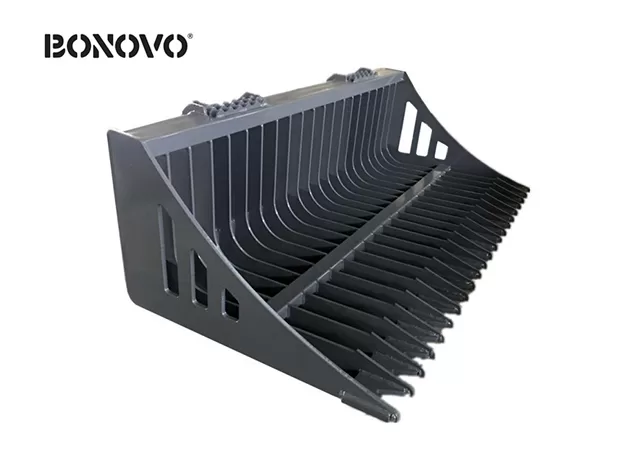
7. What Should You Look for When Selecting the Perfect Thumb for Your Excavator or Backhoe?
Choosing the perfect fit when selecting a thumb for your excavator or backhoe is crucial for getting the best performance and value. There are several key factors you need to consider to make sure you get the right thumb attachment for your specific machine and the kind of work you do. Don't just pick the first thumb you see!
First, think about compatibility. The thumb needs to be the right size for your excavator’s bucket and stick. A thumb that's too small won't be effective, and one that's too large could be clumsy or even damage your machine due to added weight or improper leverage. You'll need to know your excavator's weight class and the width of your bucket. When we design thumbs are engineered for specific machine sizes, from mini-excavators to large earthmovers. Also, consider the pin diameter and stick width if you're looking at a pin-on thumb, or the best mounting location for a weld-on thumb.
Second, decide between a mechanical thumb and a hydraulic thumb. As we discussed earlier, a mechanical thumb is simpler and more cost-effective for occasional use or consistent loads. A hydraulic excavator thumb offers superior control and flexibility and control, making it ideal for frequent use and handling various objects of different sizes. Your choice here will depend on your budget and the intensity of the work. If you're a contractor like Mark Thompson, who values efficiency, a hydraulic thumb might be the better long-term investment.
Third, look closely at the quality of construction and materials. The thumb should be made from high-strength, abrasion-resistant steel. Check the weld quality, the thickness of the steel plates, and the design of the tines. Heavy-duty construction means better durability and a longer lifespan, especially if you're working in tough conditions. Ask about the type of steel used – quality manufacturers like us at Bonovo use specialized steel to ensure our thumbs are designed for the toughest jobs. Finally, consider the ease of installation and any available warranty or after-sales support. Choosing a reputable supplier can make a big difference if you need help or spare parts down the line.
8. From Debris to Demolition: What Can You Do With an Excavator Thumb?
The number of things you can do with an excavator thumb is truly amazing! This versatile attachment turns your excavator or backhoe into a super-useful tool for all sorts of jobs, big and small. Let's look at some common applications where a thumb really shines.
One of the most popular uses is for material handling and site cleanup. Imagine you're clearing a lot. With a thumb, your excavator can easily grab and move logs, brush, stumps, and other debris. It's much faster and safer than trying to scoop these awkward items with just a bucket. The thumb holds everything securely, so you can load trucks or create neat piles without things slipping and sliding around. This is a huge help for landscaping companies, forestry operations, and even homeowners working on their property with a smaller tractor-mounted hoe.
Demolition is another area where an excavator thumb is a hero. It allows the operator to carefully dismantle structures, sort through the rubble, and separate materials like wood, metal, and concrete for recycling. The precision offered by a hydraulic thumb is especially valuable here, as it can carefully pick apart a building or grab specific pieces of debris. Construction companies also rely on thumbs for tasks like placing riprap (large rocks used to protect shorelines), setting pipes in trenches, and moving concrete barriers. The ability to lift and position heavy, irregularly shaped objects with control makes these jobs much easier and safer. The thumb makes these tough jobs more manageable.
Here's a list of common tasks:
- Land Clearing: Removing trees, stumps, brush, and rocks.
- Demolition: Tearing down structures, sorting debris.
- Construction: Moving lumber, pipes, concrete blocks, placing stones.
- Landscaping: Building retaining walls, placing boulders, moving large plants.
- Recycling: Sorting scrap metal, concrete, and other materials.
- Waste Handling: Loading and compacting waste materials.
- Forestry: Loading logs, clearing undergrowth.
- Agriculture: Clearing fence lines, moving hay bales (with appropriate grapple-like thumb designs).
No matter the industry, if you need to grab, hold, or sort materials with your excavator, a thumb is an indispensable tool.
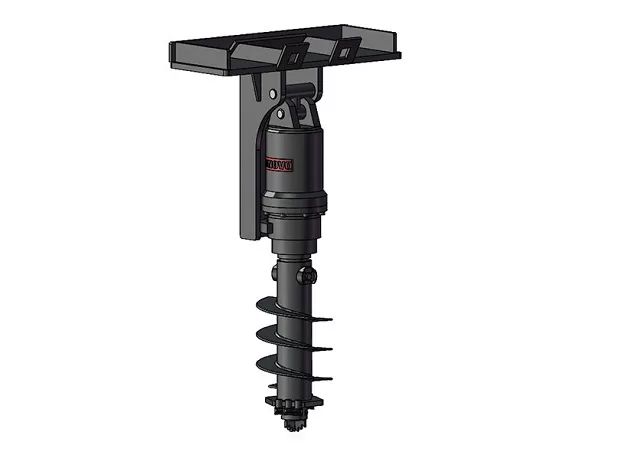
9. Keeping Your Thumb Strong: How to Maintain Your Excavator Thumb for Lasting Performance?
Once you have your excavator thumb installed, you want it to last a long time and keep working well. Just like any other part of your excavator, a little bit of care and maintenance can go a long way in keeping your thumb strong and preventing problems. Good maintenance means your thumb attachment will be ready for action whenever you need it.
First, regular inspections are key. Before you start work each day, take a quick look at your thumb. Check for any cracks in the metal, especially around the welds and pin points. Look for any bent tines or loose bolts. If you have a hydraulic thumb, check the hydraulic hoses for any leaks, cracks, or signs of wear. Also, make sure the pins that hold the thumb to the excavator’s stick and the pivot points are secure and properly greased. Greasing is super important! The pivot points on both mechanical thumbs and hydraulic thumbs need regular lubrication to prevent them from seizing up and to reduce wear. This makes adjustment smoother and extends the life of the pins and bushings.
If you do find any damage, like a crack in a weld or a bent tine, it's important to get it repaired as soon as possible. Continuing to use a damaged thumb can make the problem worse and could even lead to a failure that causes an accident or damages your excavator. For hydraulic thumbs, keeping the hydraulic system clean and the fluid at the right level is also important for smooth operation. Storing your excavator with the thumb properly folded or retracted when not in use can also help protect it from accidental damage. By following these simple maintenance tips, you can ensure your excavator thumb provides reliable service for many years, making your investment in this versatile attachment even more worthwhile. Less frequent but thorough checks by a mechanic can also catch issues early.
10. Beyond the Grip: What Other Excavator Attachments Work Well with a Thumb?
While an excavator thumb is fantastic for grabbing and holding, it's often used in conjunction with the standard digging bucket. But the true power of an excavator comes from its ability to use a wide range of attachments, and a thumb can complement many of them, or at least be part of a versatile toolkit for your machine. Understanding how a thumb fits into the broader ecosystem of Bonovo excavator attachments can help you plan your fleet's capabilities.
For instance, while a thumb works with a standard digging bucket or even an extreme-duty rock bucket for moving large rocks, sometimes you might switch out the bucket for a different attachment. A mechanical quick coupler makes changing these attachments much faster. So, you could use your excavator bucket with thumb for clearing debris, then quickly switch to a hydraulic hammer for breaking concrete, and then switch back to the bucket and thumb to clear the broken pieces. The thumb itself is an attachment, but it works with the primary attachment (usually the bucket).
Other attachments that might be used on the same excavator (though not always simultaneously with the thumb, depending on the task) include:
- Rakes: For land clearing and sifting soil. A thumb could help manage larger debris gathered by a rake.
- Grapples: Specialized for handling specific materials like logs or scrap. Some grapples are like a bucket and thumb combined into one dedicated attachment.
- Augers: For drilling holes.
- Compactors: For compacting soil in trenches.
The key is that an excavator is a platform. The thumb greatly enhances the functionality of the most common attachment – the bucket. For operators and company owners like Mark Thompson, having a suite of reliable attachments, including a robust excavator thumb, means their excavator can handle a wider range of jobs, increasing its utilization and profitability. It’s all about having the right tool for the job, and often, that tool includes a trusty thumb. Even a powerful Top Hydraulic Hammer For Excavator benefits from a thumb-equipped excavator to clear the broken material afterwards.
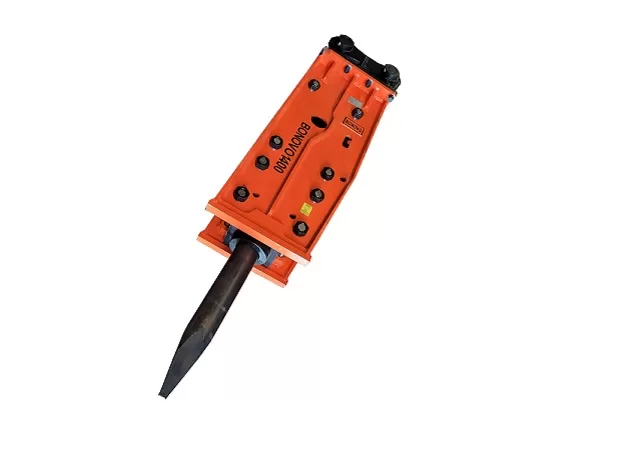
Key Takeaways: Your Excavator Thumb Essentials
An excavator thumb is a truly transformative attachment for any excavator or backhoe. Here's a quick recap of the most important things to remember:
- Boosts Versatility: A thumb allows your excavator to grab, hold, sort, and place a wide variety of materials, from logs and rocks to debris and pipes.
- Two Main Types: Choose between a simpler, more cost-effective mechanical thumb (often manually adjusted) and a more versatile, controllable hydraulic thumb (operated from the cab).
- Quality Matters: Invest in a thumb made from high-strength, wear-resistant steel with quality welds to ensure durability and safety, especially for tough jobs.
- Proper Installation: Whether it's a pin-on or weld-on thumb, correct installation is crucial for performance and safety. Ensure welds are strong and the thumb is compatible with your excavator’s bucket.
- Increases Efficiency: A thumb for excavator helps you work faster, safer, and with more precision, ultimately saving time and effort and improving productivity on the job site.
- Wide Applications: Thumbs are invaluable in construction, demolition, landscaping, forestry, and more.
- Maintenance is Key: Regular inspection, greasing of the main arm and pivot points, and prompt repairs will keep your thumb working effectively for years.
- Smart Investment: Adding a thumb is one of the best ways to maximize the capability and value of your excavator or tractor-mounted backhoe.
As a manufacturer, I've seen countless operators and companies benefit immensely from adding a quality thumb to their equipment. It's an attachment that truly punches above its weight, turning a good machine into a great one. If you're looking to enhance your excavator's functionality, an excavator thumb is an excellent choice.