The Ultimate Guide to Excavator Thumb Attachments: Boosting Versatility for Any Job with Your Mini Excavator - Bonovo
Hello, I'm Allen, and from our factory floors right here in China, we've seen firsthand how the right attachment can revolutionize a piece of construction machinery. An excavator thumb, especially for a mini excavator, is one such game-changer. This article is your comprehensive guide to understanding, selecting, and utilizing an excavator thumb to maximize your machine's potential. We'll delve into how this seemingly simple thumb attachment can significantly boost the versatility of your excavator, making tough jobs easier and more efficient. Whether you're in construction, demolition, landscaping, or even agriculture, learning about the excavator thumb is an investment in your productivity. As a manufacturer, we understand the importance of durable, high-quality equipment, and we want to share our insights to help you make informed decisions. This piece is worth reading because it’s packed with practical advice, drawn from years of manufacturing experience and customer feedback, designed to help you get the most out of your equipment.
What Exactly is an Excavator Thumb and Why Do I Need One for My Job?
An excavator thumb is a powerful attachment that mounts onto the dipper stick (or arm) of an excavator, working in conjunction with the bucket much like a human thumb works with fingers. Its primary function is to provide a clamping action, allowing the operator to grab, lift, and move objects that would be difficult or impossible to handle with just a bucket. Think about trying to pick up a log or a piece of concrete debris with just an open hand versus using your thumb and fingers – the difference in control and capability is immense. The excavator thumb brings that same level of enhanced dexterity to your machine.
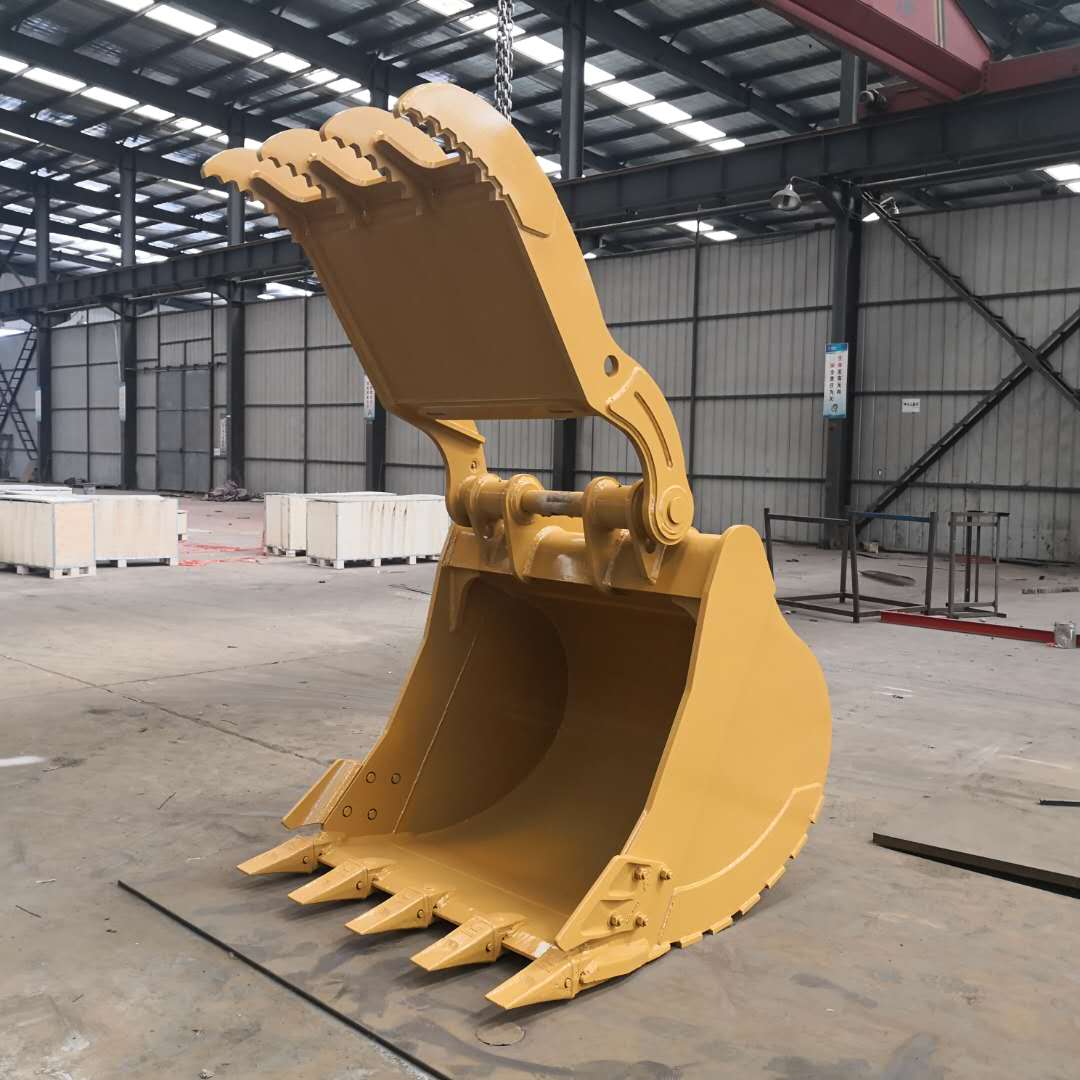
For many jobs, an excavator thumb isn't just a luxury; it's a necessity for efficiency and safety. If your job involves land clearing, demolition, scrap handling, rock placement, or pipeline work, a thumb attachment will dramatically increase your productivity. It allows the operator to securely grip and place material with precision, reducing spillage and the need for manual labor. From our perspective as manufacturers, we see companies significantly cut down on project timelines once they equip their excavators with a quality excavator thumb. It transforms your excavator can make it a truly versatile tool, capable of tackling a much wider range of tasks. This means fewer machines are needed on site, and the ones you have are working smarter, not just harder.
How Does an Excavator Thumb Transform My Mini Excavator's Performance and Versatility?
A mini excavator is already a wonderfully versatile piece of equipment, prized for its ability to work in tight spaces. Adding an excavator thumb, specifically mini excavator thumbs, elevates its performance and versatility to a whole new level. Suddenly, your compact machine can handle tasks previously reserved for larger equipment or requiring significant manual intervention. For landscaping projects, a mini excavator with a thumb attachment can easily grab and place rocks for a retaining wall, move brush and small trees, or load green waste. In demolition, it can carefully dismantle structures, sort debris, and load materials for recycling or disposal.
The transformation is particularly noticeable in how an operator can manage irregularly shaped or awkward materials. Without a thumb on an excavator, trying to balance a long pipe, a broken slab of concrete, or a bundle of branches in a bucket can be frustrating and inefficient. The excavator thumb provides that crucial opposing force, creating a secure grip. This enhanced control not only speeds up the task but also improves job site safety by minimizing the risk of materials slipping and falling. For businesses like Mark Thompson's, who aim to maximize fleet efficiency, equipping even their mini excavator fleet with excavator thumbs is a smart move towards greater productivity and profitability. It allows a single machine and operator to perform multiple functions – from digging to material handling – without needing to switch equipment or call in extra hands.
What Are the Different Types of Excavator Thumb Attachments Available? A Tip for Choosing.
When you decide to invest in an excavator thumb, you'll find there are primarily two main categories: mechanical (or manual) thumbs and hydraulic thumbs. Understanding the differences is key to choosing the right attachment for your needs. A helpful tip is to consider your typical job requirements and budget.
Mechanical excavator thumbs, often called rigid thumbs, are the simpler and generally more affordable option. They are fixed in several positions manually by adjusting a strut or pin. While they provide a good grip for many applications, they lack the on-the-fly adjustability of their hydraulic counterparts. The operator might need to get out of the cab to reposition the thumb attachment if the material size or shape changes significantly. These are a good starting point if you need a basic clamping ability and are looking for cost-effective alternatives.
Hydraulic excavator thumbs, on the other hand, are connected to the excavator's auxiliary hydraulics system. This allows the operator to open and close the thumb attachment from within the cab, offering a much greater range of motion and flexibility. Hydraulic thumbs offer superior control, making it easier to grab and manipulate a wider variety of materials with precision. Within hydraulic thumbs, you might also encounter terms like "pin-mounted and progressive link." A progressive link thumb (which we'll discuss more later) offers an even better range of motion and consistent grip pressure. While hydraulic thumbs represent a larger initial investment, the gains in productivity and versatility often provide a quick return, especially for businesses that frequently handle diverse materials. We often advise customers that if their budget allows and their work demands it, a hydraulic thumb is usually the better long-term investment.
Comparison Table: Mechanical vs. Hydraulic Thumbs
Feature | Mechanical (Manual) Thumb | Hydraulic Thumb |
---|---|---|
Adjustability | Manual, fixed positions | Hydraulic, continuous, in-cab control |
Control | Basic | Precise, excellent |
Range of Motion | Limited | Wide |
Cost | Lower initial cost | Higher initial cost |
Installation | Simpler | More complex (hydraulic lines) |
Best For | Budget-conscious, less frequent varied use | Frequent varied use, maximum productivity |
Operator Effort | May require exiting cab to adjust | Fully controlled from cab |
How Do I Pick the Right Size Excavator Thumb for My Machine and Bucket?
Selecting the correct size excavator thumb is crucial for optimal performance and to prevent damage to your machine or the attachment itself. It’s not a one-size-fits-all situation. The primary factors to consider when you pick a thumb attachment are the operating weight of your excavator, the width and capacity of your excavator bucket, and the nature of the materials you typically handle. As a rule of thumb (no pun intended!), the tip of the fully retracted excavator thumb should ideally mesh well with the bucket teeth or cutting edge when the bucket is curled in.
A thumb attachment that is too small for your bucket won't provide an effective grip on larger materials, diminishing its usefulness. Conversely, a thumb that is too large or heavy for your excavator, especially a mini excavator, can strain the machine's hydraulics, put undue stress on the excavator stick and boom, and even affect the machine's stability. It’s important to match the size and strength of the excavator thumb to the excavator's capabilities. Most manufacturers, including us at BONOVO, will provide compatibility charts or recommendations based on excavator model and bucket dimensions. Always consult these guides or speak directly with your supplier. Providing your machine specifications will help us recommend the perfect size excavator thumb from our extensive Excavator Attachments range.
Can I Install an Excavator Thumb Attachment Myself, or Should I Seek Professional Help to Install It?
The installation process for an excavator thumb can vary in complexity, largely depending on whether you choose a mechanical or hydraulic thumb, and your own technical proficiency. Many mechanically inclined operators or maintenance personnel can successfully install an excavator thumb. However, it’s not a task to be taken lightly, as incorrect installation can lead to performance issues or safety hazards.
For a mechanical thumb, the installation usually involves welding a base plate to the excavator stick and then pinning the thumb and its positioning arm to this plate. This requires good welding skills and an understanding of proper placement to ensure the thumb functions correctly with the bucket. For a hydraulic thumb, the process is more involved. In addition to the mechanical mounting, you'll need to connect the thumb's hydraulic cylinders to the excavator's auxiliary hydraulics. This includes running hydraulic hoses, ensuring correct connections, and sometimes installing additional control valves or wiring if the machine isn't already equipped for a hydraulic attachment. If you're not confident in your welding abilities or familiar with excavator hydraulics, it's highly advisable to seek professional help. A qualified technician will ensure the thumb attachment is installed securely, the hydraulics are correctly integrated, and everything operates safely. While DIY can save on initial costs, a professional install guarantees peace of mind and proper functionality from the get-go. Remember, safety and correct operation are paramount.
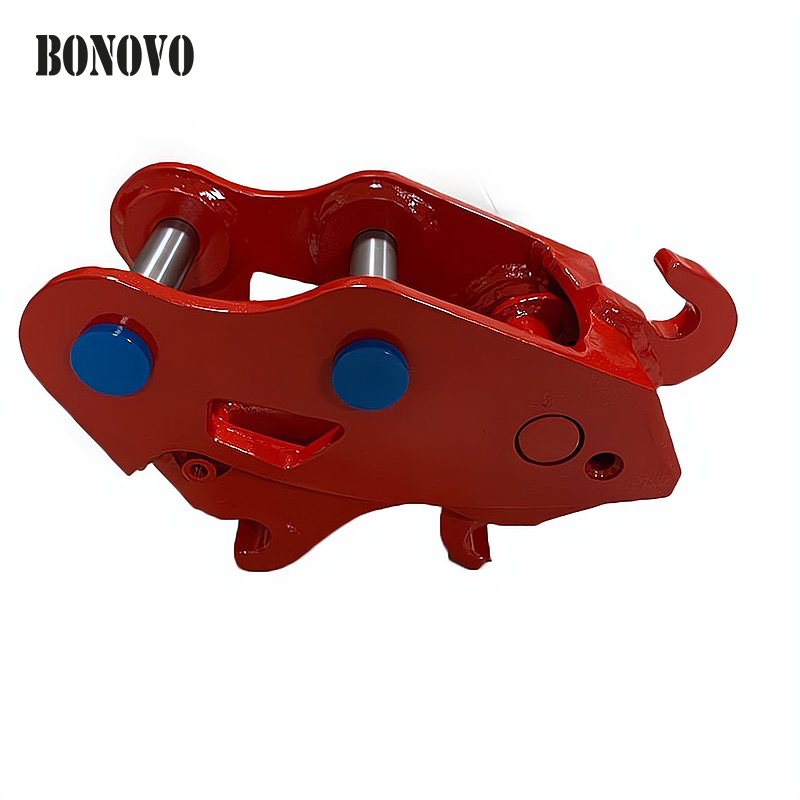
What Key Material and Design Features Indicate a Quality Thumb Attachment?
When investing in an excavator thumb, understanding the key material and design features that signify quality is crucial for ensuring durability and performance. As a factory, we place immense emphasis on these aspects. The material used is paramount. High-strength, wear-resistant steel, such as AR400 or AR500, is the gold standard for the tines and body of the thumb attachment. This type of material can withstand the abrasion and impact common in demolition, rock handling, and other demanding applications, ensuring a longer service life for the excavator thumb.
Beyond the primary material, look at the design details.
- Robust Tine Design: The tines should be thick and well-gusseted for strength. The shape and spacing of the tines affect how well the thumb can grip different types of material. Some designs feature serrated edges for an even better grip.
- Quality Pins and Bushings: The pivot points of an excavator thumb are subject to significant stress. Hardened steel pins and replaceable bushings are essential to reduce wear and allow for easier maintenance.
- Weld Quality: Inspect the welds. They should be clean, consistent, and show good penetration. Poor welds are a common failure point in low-quality attachments.
- Reinforcement: Critical stress areas should be reinforced. This might include extra plating or strategic bracing in the design.
A well-designed excavator thumb will not only be strong but also engineered to mesh effectively with the excavator bucket across its range of motion. This attention to design and material quality is what separates a reliable, long-lasting attachment from one that might fail prematurely, leading to costly downtime – a major concern for fleet managers like Mark Thompson.
How Does a Progressive Link Excavator Thumb Enhance Versatility and Grip?
Among hydraulic thumbs, the progressive link thumb (sometimes called a linkage thumb) represents a significant step up in performance and versatility. The "progressive link" design refers to a specific linkage system between the hydraulic cylinder, the excavator stick, and the thumb itself. This design allows the excavator thumb to maintain a more consistent grip and follow the bucket through a wider range of motion – often up to 180 degrees or more. This is a distinct advantage over standard direct-pin hydraulic thumbs offer, which can sometimes lose their optimal grip angle as the bucket curls.
The primary benefit of a progressive link thumb is its ability to pick up and grab objects of various sizes and shapes much closer to the excavator. It can also curl up tighter against the stick when not in use, providing better visibility and a more compact profile. This extended range of motion means the operator can manipulate material with greater precision and flexibility, making tasks like sorting debris, delicate placement of rocks in landscape projects, or handling logs more efficient. While progressive link thumbs might have a slightly higher upfront cost, the enhanced productivity and superior material handling capabilities they offer often justify the investment for serious professionals. For businesses that demand maximum versatility and efficiency from their excavator attachment lineup, a progressive link thumb is an excellent option. Consider how an Excavator Bucket with Thumb featuring a progressive link can streamline your operations.
What Maintenance Tips Will Keep My Mini Excavator Thumb in Top Condition?
Proper maintenance is key to ensuring your excavator thumb, especially a mini excavator thumb, enjoys a long, productive life and continues to perform at its best. Regular maintenance also helps prevent unexpected breakdowns, which can be costly in terms of both repairs and project delays. Fortunately, excavator thumb maintenance is generally straightforward. The first tip is to incorporate thumb checks into your daily machine walk-arounds.
Here are some key maintenance practices:
- Regular Inspection: Visually inspect the excavator thumb daily for any signs of wear, cracks in welds, or damage to the tines. Check the mounting points to ensure all bolts and pins are secure. For hydraulic thumbs, inspect hoses for leaks, cracks, or abrasions, and check cylinder seals.
- Lubrication: All pivot points, including the main pin connecting the thumb to the stick and any linkage pins (especially on progressive link thumbs), should be greased regularly according to the manufacturer's recommendations. Proper lubrication reduces friction and wear.
- Check Pins and Bushings: Worn pins and bushings can lead to sloppy movement and put additional stress on the thumb attachment and the excavator arm. Replace them as needed. This is a common wear item.
- Hydraulic System Care (for hydraulic thumbs): Ensure the excavator's hydraulic system is well-maintained, with clean oil and filters. Contaminated hydraulics can damage the thumb's cylinder and control valves.
- Cleaning: Keeping the excavator thumb clean, especially around pivot points and hydraulic components, can help you spot potential issues earlier.
Addressing small issues promptly can prevent them from escalating into major repairs. For example, a small crack in a weld, if caught early during an inspection, can often be easily repaired. Left unattended, it could lead to a catastrophic failure of the thumb attachment. Investing a little time in maintenance will pay dividends in reliability and longevity for your excavator thumb.
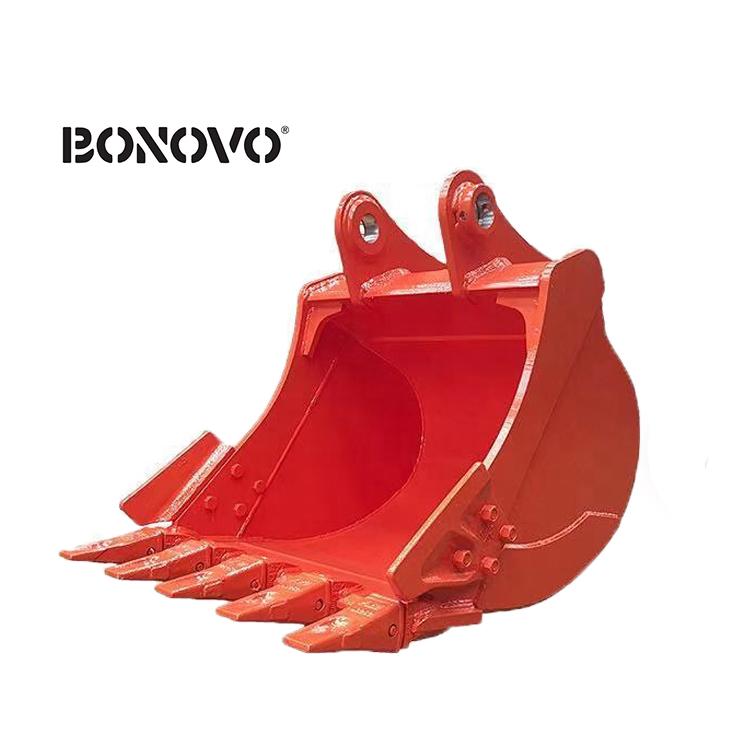
Where Can I Find Reliable Excavator Thumbs and What Should I Ask Suppliers Before I Pick?
Finding a reliable supplier for your excavator thumb is just as important as choosing the right type of thumb. Whether you're looking for a thumb attachment for a large hydraulic excavator or specifically mini excavator thumbs, you want a product that's built to last and a supplier who stands behind it. Mark Thompson often finds suppliers through exhibitions and Google searches, which are excellent starting points. When you identify potential suppliers, especially when considering sourcing from factories like ours in China, there are several key questions you should ask before you pick an option.
First, inquire deeply about the material specifications. Ask for details on the type of steel used (e.g., Q345B, NM400, Hardox). High-quality, wear-resistant steel is non-negotiable for a durable excavator thumb. Next, discuss the design and manufacturing process. Are critical stress points reinforced? What is their welding standard? Can they provide technical drawings or specifications? Compatibility is another major concern. Confirm that the excavator thumb will correctly fit your specific excavator model and bucket. Provide your machine's make, model, and bucket dimensions to ensure a proper match.
Don’t forget to ask about warranty and after-sales service. What does the warranty cover, and for how long? What is their process for handling claims? Can they supply spare parts like pins and bushings readily? Lead times for delivery are also important, especially if you have an urgent job. Finally, discuss communication. As Mark Thompson sometimes experiences, inefficient communication can be a pain point. Ensure the supplier has responsive and knowledgeable sales representatives who can answer your technical questions clearly. At BONOVO, we pride ourselves on transparent communication and providing all necessary technical details to ensure our customers, whether they are large construction companies or equipment rental businesses, get the perfect excavator thumb for their needs. We understand that purchasing an attachment is an investment, and we aim to make it a smooth and confident process.
Beyond Thumbs: What Other Attachments Complement an Excavator's Versatility?
While an excavator thumb significantly boosts your machine's versatility, it's often just one piece of the puzzle in creating a truly multi-functional excavator. Several other attachments can work in conjunction with or independently of a thumb to further enhance your excavator's capabilities, allowing it to tackle an even broader spectrum of tasks. Understanding these options can help you build an attachment arsenal that maximizes your return on investment for your excavator, including your mini excavator.
- Quick Couplers: Perhaps one of the most important complementary attachments is a High-quality mechanical quick coupler from BONOVO. A quick coupler allows the operator to change between various attachments – like different buckets, a thumb, a grapple, or a hydraulic hammer – quickly and safely, often without leaving the cab. This dramatically reduces downtime when switching tasks and is almost essential for maximizing the versatility an excavator can make.
- Specialized Buckets: While a general-purpose bucket works well with an excavator thumb for many tasks, specialized buckets like trenching buckets, grading buckets, or even rock buckets can further optimize performance for specific jobs. A thumb can still be used with many of these to handle dislodged material.
- Grapples: For dedicated material handling, especially in demolition, forestry, or recycling, a hydraulic grapple might be chosen over an excavator thumb and bucket combination. However, for many, an excavator thumb offers a more versatile solution as it allows for both digging and grabbing.
- Hydraulic Hammers/Breakers: For demolition of concrete or rock excavation, a hydraulic hammer is indispensable. While not directly used with a thumb, the ability to quickly switch to a hammer and then back to a bucket and thumb (thanks to a quick coupler) makes the excavator a powerhouse.
- Augers: For drilling holes for posts, fences, or tree planting, an excavator auger attachment is perfect.
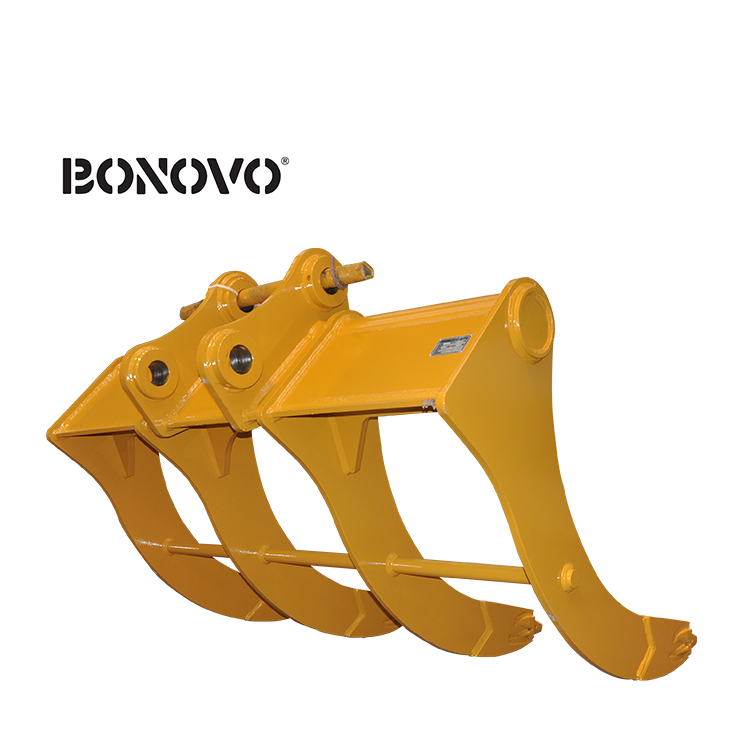
The key is to analyze the range of tasks your excavator needs to perform and strategically select attachments that provide the most flexibility and productivity. An excavator thumb is a fantastic starting point for enhancing versatility, and when combined with other well-chosen attachments, it can truly transform your machine into a multi-purpose workhorse, ready for almost any job site challenge. This approach aligns perfectly with the goals of efficiency-minded business owners like Mark Thompson, who seek to get the most out of their equipment fleet.
Key Takeaways: Maximizing Your Excavator's Potential with a Thumb Attachment
Investing in an excavator thumb is a smart decision for anyone looking to enhance the versatility, efficiency, and productivity of their excavator, particularly a mini excavator. Here’s a quick recap of the most important points to remember from our discussion:
- Enhanced Capability: An excavator thumb acts like your machine's own thumb, allowing it to grab, hold, and manipulate a wide variety of materials that a bucket alone cannot handle efficiently.
- Types Matter: Choose between mechanical (manual) thumbs for basic, cost-effective solutions, or hydraulic thumbs (including progressive link thumbs) for superior control, range of motion, and on-the-fly adjustability.
- Sizing is Crucial: Always match the size of the excavator thumb to your excavator model and bucket to ensure optimal performance and safety. Consult manufacturer guidelines.
- Quality Pays: Look for excavator thumbs made from high-strength, wear-resistant steel with quality pins, bushings, and robust design features. This ensures longevity and reliability.
- Installation Considerations: While some may DIY a mechanical thumb install, hydraulic thumb installation is more complex. Professional installation is often recommended to ensure safety and proper function.
- Maintenance is Key: Regular inspection, lubrication, and prompt attention to wear and tear will keep your excavator thumb attachment in top working order.
- Supplier Diligence: Ask potential suppliers detailed questions about material specs, design, compatibility, warranty, lead times, and after-sales support. Clear communication is vital.
- Beyond the Thumb: Consider other attachments like quick couplers and specialized buckets to further expand your excavator's capabilities, making it a truly versatile tool on any job site.
As a manufacturer committed to providing high-quality excavator attachments, we at BONOVO have seen countless operations transformed by the simple addition of a well-chosen excavator thumb. It’s an attachment that offers a significant return on investment by enabling your machine and operator to do more, faster, and safer. If you have any questions or need guidance in selecting the perfect excavator thumb or any other excavator attachment for your specific needs, please don't hesitate to reach out. We're here to help you get the job done right.