Unlock Peak Efficiency: Your Guide to Mechanical Pin Grabber Quick Couplers for Excavators (Mini to Heavy Ton Machines) - Bonovo
Switching attachments on your excavator can be a time-consuming chore, eating into valuable project time and potentially impacting your bottom line. Imagine effortlessly swapping your digging bucket for a hydraulic hammer or a grapple in minutes, not hours. That's the power a mechanical pin grabber coupler brings to your excavator. This guide dives deep into these essential tools, exploring how they work, their safety features like the dual lock system, and why choosing the right coupler is vital for maximizing the efficiency and versatility of your excavator, from a compact mini excavator up to large tonnage machines. If you rely on heavy equipment, understanding how a quick coupler can streamline your attachment changes is crucial for staying competitive. Let's explore how this pin grabber technology can revolutionize your jobsite workflow.
What Exactly is a Mechanical Pin Grabber Coupler? An Overview.
At its core, a mechanical pin grabber coupler is a device fitted to the end of an excavator's arm (dipper stick) that allows the operator to connect and disconnect various attachments much faster than traditional direct pinning methods. Think of it as a universal adapter for your machine's tools. Instead of manually hammering out two heavy bucket pins each time you need to switch from digging to breaking or grading, the coupler uses a mechanical system – usually involving a lever and a spring or locking bar – to secure the attachment's pins.
The "pin grabber" part of the name refers specifically to its design, which uses hooks or jaws to 'grab' the existing pins on the bucket or other attachment. This means, in many cases, you don't need specialized attachments; the coupler is designed to work with standard OEM pin configurations. This versatility is a major advantage, especially for fleet owners like Mark Thompson who might have a variety of existing buckets and tools. The primary goal is simple: dramatically reduce the time and effort required for attachment changes, boosting overall jobsite productivity. This product essentially transforms your single-task machine into a multi-functional tool carrier.
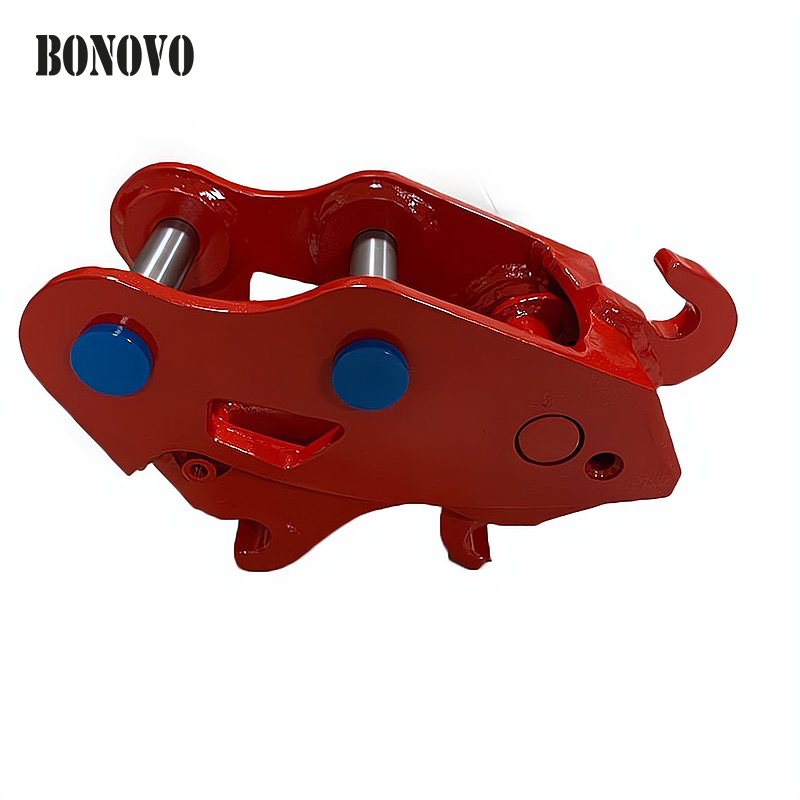
This overview highlights the fundamental function – speed and convenience. It eliminates the often strenuous and sometimes hazardous task of manually aligning heavy attachments and driving pins in and out. For businesses involved in construction, demolition, landscaping, or any field requiring frequent attachment swaps, the time savings translate directly into cost savings and increased operational efficientcy. The mechanical nature means it doesn't require auxiliary hydraulics, simplifying installation and maintenance compared to fully hydraulic systems.
How Does the Pin Grabber Mechanism Work?
The magic of a mechanical pin grabber coupler lies in its relatively simple yet robust mechanism. Unlike hydraulic couplers that use hydraulic flow from the excavator to actuate the locking mechanism, mechanical couplers rely on manual force and clever engineering. Typically, the operator uses a dedicated lever or tool (often resembling a large wrench or bar) provided with the coupler.
Here's a general breakdown of the process:
- Positioning: The operator positions the excavator arm so the coupler is ready to engage the first pin (usually the front pin) of the attachment.
- Engagement: The coupler often has a fixed hook or jaw designed to capture the first pin. The operator curls the coupler to securely seat this pin.
- Activation: The operator inserts the operating lever into a specific socket on the coupler. Applying force to this lever retracts the locking mechanism (often a sliding jaw or spring-loaded bar) against spring pressure.
- Securing: While the locking mechanism is retracted, the operator adjusts the coupler position to align the mechanism with the second pin of the attachment.
- Locking: The operator carefully removes the lever. The spring force automatically drives the locking mechanism forward, securing the second pin and ensuring the attachment is firmly locked in place. A visual indicator or safety latch often confirms engagement.
To release the attachment, the process is reversed. The operator uses the lever to again overcome the spring force, retracting the locking mechanism and allowing the second pin to be freed. Then, the first pin can be disengaged. This manual system is straightforward, reliable, and eliminates the need for additional hydraulic lines running down the dipper stick solely for the coupler. The design focuses on secure pin grabbing, ensuring a tight fit.
Why is the Dual Lock System a Critical Safety Feature?
Safety is paramount on any jobsite, and the potential for an attachment to accidentally detach from an excavator is a significant risk. This is where the dual lock system, a common feature on modern mechanical pin grabber couplers, becomes absolutely essential. It provides redundant locking mechanisms to drastically minimize the chance of unexpected release.
The core principle of a dual lock system involves securing both the front and rear attachment pins independently. Here’s how it typically works:
- Primary Lock: This usually involves the fixed hook or jaw that captures the first pin when the operator initially curls the coupler into the attachment. This provides the initial connection point.
- Secondary Lock: This is the active locking mechanism, often a spring-actuated jaw or bar, that engages the second pin when the operator uses the lever. This mechanism applies constant spring force to keep the second pin secured.
The critical safety aspect is that even if one part of the locking system were somehow compromised (which is highly unlikely in a well-maintained coupler), the other lock continues to secure the attachment. Some advanced designs incorporate additional safety features, such as a manual safety pin that must be inserted after the mechanical lock is engaged, providing a third layer of security. This feature reduces the likelihood of releasing your attachment unexpectedly, a major concern addressed by reputable manufacturers in the industry. For decision-makers like Mark, knowing the coupler prioritizes safety through a reliable dual lock system is a non-negotiable requirement.
Furthermore, many modern couplers incorporate visual indicators. These might be colored tabs or pins that clearly show the operator whether the secondary lock is fully engaged or not, allowing for quick verification from the cab or ground level before starting work. This dual approach – securing both pins and providing clear visual confirmation – is fundamental to safe quick coupler operation.
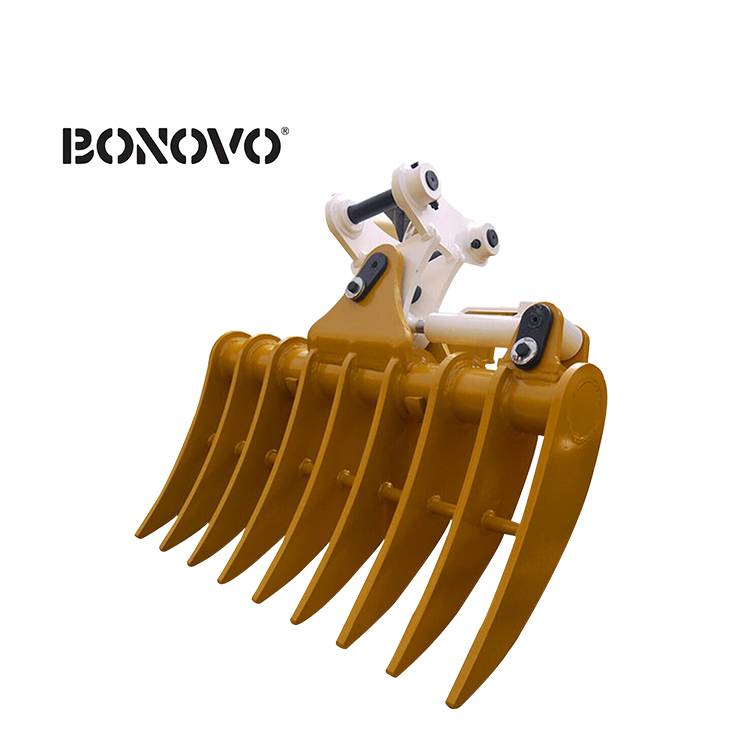
What are the Main Benefits of Using a Quick Coupler on Your Excavator?
Integrating a quick coupler, especially a robust mechanical pin grabber coupler, onto your excavator offers a multitude of advantages that directly impact efficiency, versatility, and potentially profitability. For fleet managers and company owners, these benefits are compelling:
- Massively Reduced Downtime: This is the most significant advantage. Swapping attachments manually can take anywhere from 15 minutes to over an hour, depending on the attachment, conditions, and operator skill. A quick coupler cuts this down to mere minutes, sometimes even less than five. Less downtime means more time working.
- Example: Switching from a digging bucket to a hydraulic hammer might take 30+ minutes manually. With a coupler, it's often under 5 minutes.
- Increased Machine Versatility: An excavator equipped with a coupler can quickly adapt to various tasks on the jobsite. Digging, breaking, grading, material handling – the machine becomes a multi-tool platform, maximizing its utilization rate. You can use the right tool for the job, improving overall project quality and speed.
- Enhanced Operator Safety: Eliminating the need to manually hammer heavy pins in and out reduces the risk of injuries from slips, trips, strained muscles, or flying metal fragments. The operator often performs the change using the lever, minimizing direct handling of heavy components. The dual lock system further enhances operational safety.
- Improved Efficiency: Faster attachment changes mean less idle time for both the machine and the operator. This translates to more work completed per shift, potentially shortening project timelines and reducing operational costs. The ability to always use the optimal attachment also makes tasks more efficient.
- Potential for Reduced Fleet Size: In some scenarios, the increased versatility offered by a coupler might allow one machine to perform tasks that previously required two separate machines, potentially leading to savings in equipment acquisition and maintenance costs.
These benefits apply across a range of machine sizes, from a mini excavator performing delicate landscaping tasks to a large tonnage machine on a heavy construction site. The investment in a quality coupler often provides a rapid return through increased productivity and safety.
Mechanical vs. Hydraulic Pin Grabber Couplers: Which is Right for You?
Choosing between a mechanical and a hydraulic pin grabber coupler depends on several factors, including budget, machine size, frequency of attachment changes, and operational preferences. Both systems aim to achieve the same goal – fast attachment switching – but they go about it differently.
Mechanical Pin Grabber Couplers:
- Pros:
- Lower Initial Cost: Generally less expensive to purchase than hydraulic counterparts.
- Simpler Design: Fewer moving parts, no hydraulic hoses or cylinders specific to the coupler, potentially leading to lower maintenance needs.
- Easier Installation: Doesn't require tapping into the excavator's hydraulic system.
- Reliable: Robust mechanical locking mechanisms, often featuring dual lock safety.
- Cons:
- Manual Operation: Requires the operator to exit the cab (or reach from the cab on very small machines) and use a lever or tool to release and lock the attachment. This takes slightly longer than hydraulic operation.
- Physical Effort: Requires some physical force to operate the lever.
Hydraulic Pin Grabber Couplers:
- Pros:
- Convenience: Allows the operator to change attachments without leaving the cab, using switches to control the hydraulic pin engagement/disengagement. This is the fastest method.
- Reduced Effort: No manual lever operation required.
- Cons:
- Higher Initial Cost: More expensive due to the hydraulic components (cylinders, valves, hoses).
- More Complex Installation: Requires connecting to the excavator's auxiliary hydraulic circuit. Pressure requirement before hydraulic oil flows needs consideration.
- Increased Maintenance Potential: More components (seals, hoses, cylinders) that could potentially leak or fail over time. Requires managing hydraulic flow.
- Safety Considerations: Requires careful operation to avoid accidentally bumping the wrong switch in the cab. Many modern hydraulic systems have multi-stage activation sequences (e.g., upgraded two-stage control system where the first requires the operator to press and hold one button, then press the second button within two seconds to activate release) to prevent accidental disconnect. These systems use system pressure against the integrated coupler's cylinder.
For many users, particularly those like Mark Thompson who value reliability, competitive pricing, and straightforward maintenance, the mechanical pin grabber coupler (similar in concept to a manual quick hitch) offers an excellent balance. It provides the core benefit of quick attachment changes with proven safety features like the dual lock system, without the added complexity and cost of hydraulics. The decision often comes down to weighing the convenience of in-cab operation against the simplicity and cost-effectiveness of a mechanical system.

Are Mechanical Couplers Compatible with Different Excavator Buckets and Attachments?
Compatibility is a major concern for equipment owners. The good news is that most mechanical pin grabber couplers are designed with versatility in mind, aiming to fit standard attachments conforming to the excavator's original pin specifications. However, it's not always plug-and-play, and careful attention to dimensions is crucial.
Key factors determining compatibility include:
- Pin Diameter: The coupler's hooks and locking mechanism are designed for specific pin diameters. Most couplers are built for the standard pin size of the excavator weight class (e.g., 80mm pins for a 20-ton machine). Ensure your attachment pins match the coupler's specification.
- Pin Center-to-Center Distance: This is the distance between the center of the front pin and the center of the rear pin on the attachment. The coupler has a specific range it can accommodate.
- Dipper Stick Width (Ear Width): This is the distance between the mounting bosses on the attachment where the pins go through. The coupler must fit snugly between these bosses.
Reputable manufacturers like BONOVO understand these challenges. We often design our mechanical pin grabber couplers to handle slight variations in pin centers, increasing compatibility across different attachment brands. Some advanced pin grabber designs can even accommodate multiple pin diameters within a certain range. However, it's always best practice to verify the specification of both the coupler and the attachments you intend to use. Providing your supplier with the exact make and model of your excavator and details about your main attachments (especially non-OEM ones) is vital.
As a factory specializing in these products, we, at BONOVO, maintain extensive databases of machine and attachment specifications. When a customer like Mark inquires about a coupler, we work closely with them to confirm the dimensions of their machine and key attachments, such as Excavator Bucket Pins, to ensure a proper fit. This avoids frustrating compatibility issues upon delivery and ensures the coupler functions safely and efficiently from day one. While many standard buckets will attach without issue, always double-check dimensions before purchasing.
How Do You Operate a Manual Quick Hitch Safely?
Operating a manual quick hitch or mechanical pin grabber coupler is straightforward, but following correct procedures is essential for safety and preventing damage to the equipment or attachment.
Here’s a step-by-step guide emphasizing safety:
- Prepare the Area: Ensure the ground is relatively level and clear of obstructions and personnel. Position the attachment securely on the ground.
- Engage the First Pin: Slowly maneuver the excavator arm to align the coupler's fixed front hook/jaw with the attachment's front pin. Curl the coupler to securely grab this pin. Lift the attachment slightly off the ground to confirm engagement.
- Retract the Locking Mechanism: Safely exit the cab (or reach if possible/safe on a mini digger). Insert the operating lever into the designated socket on the coupler. Apply steady force to the lever to retract the rear locking mechanism against its spring pressure. Be mindful of pinch points and maintain firm footing.
- Engage the Second Pin: While holding the locking mechanism retracted with the lever, slowly adjust the excavator's curl function to align the retracted mechanism with the rear pin of the attachment.
- Lock the Coupler: Carefully and smoothly release the pressure on the lever, allowing the spring-loaded locking mechanism to engage the rear pin. Remove the lever.
- VERIFY ENGAGEMENT (CRITICAL STEP):
- Visual Check: Look closely at the coupler. Check any visual indicators (e.g., colored tabs, pin position) to confirm the lock is fully engaged. Ensure the locking bar or jaw is properly seated against the rear pin.
- Physical Check: Gently curl the attachment inwards and outwards, and roll it slightly against the ground. There should be no excessive movement or rattling indicating a loose connection. The attachment should feel securely locked in place.
- Safety Pin (If Applicable): If the coupler design includes a manual safety pin, insert it now according to the manufacturer's instructions. This provides an extra layer of safety.
- Proceed with Work: Only after confirming the attachment is securely locked should you resume normal operation.
To release the attachment, reverse the process: remove the safety pin (if used), use the lever to retract the lock, lower the attachment safely to the ground, disengage the rear pin, then disengage the front pin. Never attempt to operate the lever while the attachment is suspended high in the air or over personnel. Proper training and adherence to these steps are key to preventing accidents, especially releasing your attachment unexpectedly.
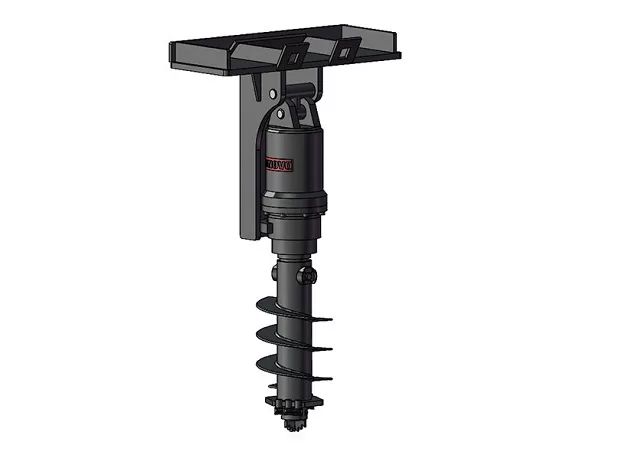
What Should You Look for When Choosing a Mechanical Pin Grabber Coupler Manufacturer?
Selecting the right manufacturer for your mechanical pin grabber coupler is just as important as choosing the right type of coupler. For discerning buyers like Mark Thompson, who prioritize quality and reliability alongside competitive pricing, several factors come into play:
- Material Quality and Construction: Ask about the type of steel used. High-strength, wear-resistant steel (like NM400/NM500 or Hardox equivalents in critical areas) is essential for durability, especially in the locking components and body. Check the weld quality and overall robustness of the design. Does the manufacture process meet international standards?
- Safety Features: Does the coupler incorporate a proven dual lock system? Are there clear visual indicators for engagement? Does it include a manual safety pin option? Safety certifications or compliance with industry standards (like ISO standards) are positive signs.
- Compatibility Guarantee: Does the company have a process to ensure the coupler will fit your specific excavator model and main attachments? Do they request detailed measurements (pin diameters, centers, dipper width)? A good supplier will work with you to guarantee fit. BONOVO, for example, prides itself on this verification process.
- Design and Ease of Use: Is the locking mechanism well-designed for easy operation with the provided lever? Is the coupler relatively compact to maintain breakout force? Look for designs that minimize complexity while maximizing strength.
- Warranty and After-Sales Support: What warranty is offered? Is the company responsive? Can they provide technical support or spare parts (like replacement springs or levers) if needed? This is crucial for minimizing potential downtime. Access to spare parts is a common pain point Mark worries about.
- Reputation and Experience: How long has the company been manufacturing excavator attachments? Do they specialize in couplers? Look for reviews, testimonials, or case studies. Attending exhibitions, as Mark does, is a great way to meet suppliers like BONOVO face-to-face and assess their product quality and expertise firsthand. BONOVO offers a wide range of Excavator Attachments built on years of manufacturing experience.
- Available Sizes: Ensure the manufacturer offers a coupler specifically designed for your excavator's tonnage class. A one-size-fits-all approach rarely works well.
Choosing a manufacturer based solely on the lowest price can be risky. Investing in a well-built coupler from a reputable company that prioritizes quality, safety, and customer support will likely provide better long-term value and peace of mind.
Can a Quick Coupler Improve Productivity on a Mini Excavator or Mini Digger?
Absolutely. While quick couplers are beneficial for excavators of all sizes, they offer particularly significant advantages for mini excavators (typically under 8 ton) and mini diggers. These smaller machines are often used in applications requiring frequent attachment changes, such as:
- Landscaping: Switching between trenching buckets, grading buckets, augers, grapples, and compactors.
- Utility Work: Alternating between narrow buckets for trenches, pavement breakers, and standard digging buckets.
- Plumbing and Electrical: Using various small buckets and potentially breakers or augers in tight spaces.
- Demolition (Small Scale): Swapping between a bucket, hammer, and sorting grapple.
On a mini excavator, manual attachment changes can be disproportionately time-consuming relative to the actual task duration. Adding a mechanical pin grabber coupler allows the operator to swap tools quickly and easily, often without even needing assistance. This dramatically improves the workflow. Imagine needing to dig a small trench (trenching bucket), drill a hole for a post (auger), and then smooth the area (grading bucket) – a coupler makes this sequence seamless.
The time saved translates directly into more tasks completed per day, increasing the mini excavator's overall productivity and profitability. Furthermore, the ease of changing attachments encourages the operator to always use the best tool for the immediate task, rather than "making do" with a suboptimal attachment to avoid the hassle of changing it. This improves the quality of work and can reduce wear and tear on both the machine and the attachments. A Mechanical Quick Coupler is often one of the best investments a mini excavator owner can make.
Maintaining Your Mechanical Coupler: Tips for Longevity and Performance.
A mechanical pin grabber coupler is a robust piece of equipment, but like any mechanical device, it requires regular maintenance to ensure safe operation, longevity, and optimal performance. Neglecting maintenance can lead to premature wear, potential malfunction, and costly downtime. Here are key maintenance tips:
- Regular Greasing: Identify all grease points (zerks) on the coupler. These typically lubricate the moving parts of the locking mechanism and pivot points. Follow the manufacturer's recommended greasing schedule (often daily or every 10 operating hours) using the specified type of grease. Proper lubrication reduces friction and wear.
- Visual Inspections: Before each use, perform a quick visual inspection. Look for:
- Cracks in welds or the main body.
- Excessive wear on the fixed hooks and moving locking jaw/bar.
- Damage to the operating lever socket.
- Ensure the visual lock indicators (if present) are functioning correctly.
- Check that the spring mechanism appears intact and provides strong force.
- Check for Looseness: Periodically check the connection between the coupler and the attachment after it's locked. There should be minimal play. Excessive movement could indicate wear on the coupler's jaws or the attachment's pins. Also, check the pins connecting the coupler to the excavator arm.
- Cleanliness: Keep the coupler relatively clean, especially around the locking mechanism. Dirt and debris buildup can interfere with proper operation and accelerate wear.
- Operating Lever Care: Inspect the operating lever for bends or damage. Ensure it fits correctly into the socket.
- Listen for Unusual Noises: Pay attention to any strange grinding or clicking sounds during operation, which could indicate an internal issue.
- Follow Manufacturer Guidelines: Always refer to the specific maintenance manual provided by the coupler manufacturer for detailed instructions and schedules.
Consistent maintenance is simple but crucial. It ensures the dual lock safety system functions as intended, prevents unexpected failures, and extends the service life of your investment. Addressing small issues early prevents them from becoming major problems later. A well-maintained BONOVO Attachment like a mechanical coupler will provide years of reliable service.
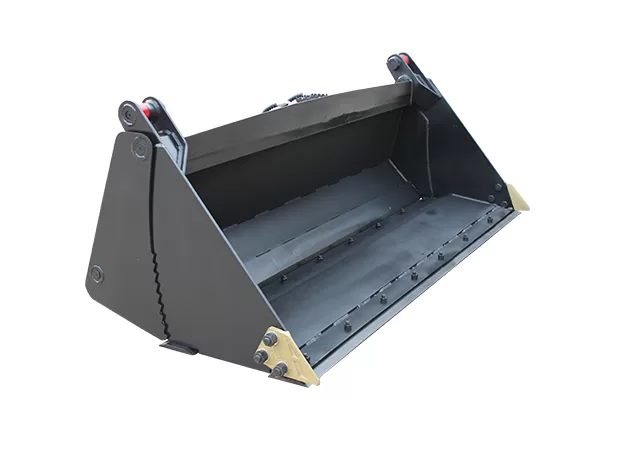
Key Takeaways:
- Efficiency Boost: Mechanical pin grabber couplers drastically reduce attachment change time, significantly increasing excavator productivity.
- Enhanced Safety: Dual lock systems are critical, securing both attachment pins to prevent accidental release. Always visually verify lock engagement.
- Increased Versatility: Quickly switch between buckets, breakers, grapples, and other tools, making your excavator a multi-tasking powerhouse.
- Mechanical Simplicity: Offers a reliable and cost-effective solution compared to hydraulic couplers, with easier installation and maintenance.
- Compatibility is Key: Always verify pin diameters, pin centers, and dipper width with the manufacturer to ensure a proper fit for your machine and attachments.
- Choose Wisely: Select a manufacturer based on quality materials, robust design, proven safety features, warranty, and support – not just price.
- Maintenance Matters: Regular greasing and visual inspections are vital for safe operation and longevity.